In the process of metal cutting, a large amount of heat will be generated at the interface between metal and tool, and its temperature can reach 600~1000 ℃. This has a great impact on the surface quality of the workpiece, dimensional accuracy, tool service life, kinetic energy consumption and production efficiency. The use of cutting fluid can take away the heat generated by cutting in a timely manner. The scouring effect of large flow of cutting fluid can make the chips break away from the machined surface in a timely manner, and clean the fixture and machine tool guard, so that the workpiece can achieve good processing quality. Effect of three process parameters of emulsion on aluminum alloy processing In the process of aluminum alloy cutting, the concentration, pressure and flow of emulsion have a great impact on the processing quality of parts. 1. Concentration selection of emulsion The cutting fluid used in the factory site is the working fluid diluted by cutting fluid concentrate and water. There are two methods to indicate the effective content of cutting fluid: concentration and dilution ratio. The refractometer is used for on-site rapid detection of the concentration of the stock solution, while the titration method is generally used for laboratory detection. Only when the concentration of the working fluid is maintained within the specified range can the cutting fluid play its due role. If the concentration of cutting fluid is too low, it is easy to rust, increase tool wear and reduce processing quality, as well as decline in antibacterial performance, easy to rot and stink. On the contrary, if the concentration of cutting fluid is too high, it will not only increase the processing cost, but also lead to a series of problems such as decreased cleaning and cooling ability of cutting fluid, decreased defoaming ability, irritation to the eyes and respiratory tract of operators, and skin allergy. Therefore, maintaining the proper concentration of cutting fluid is an important part of water-based cutting fluid management. Generally, concentration inspection is regarded as an important indicator of cutting fluid management. Open cutting methods, such as turning and milling, are smooth in chip removal. The cutting fluid is mainly used for cooling and chip cleaning, and has low requirements for concentration. Generally, the cutting fluid with concentration of about 3%~5% is selected. When cutting in closed situations, such as drilling and tapping, the processing environment is bad, the chip removal is not smooth, and the tool and workpiece are squeezed each other. At this time, the cutting fluid should cool and lubricate the tool, and also flush the chip. This processing method requires high lubricating performance of the cutting fluid. Generally, the cutting fluid with a concentration of 5%~8% is selected for drilling. When tapping, the workpiece is seriously squeezed by the tool, so it is appropriate to select the cutting fluid with the concentration of extreme pressure additives of 8%~10%. Proper selection of metal cutting fluid can not only reduce cutting temperature, reduce tool wear, extend tool life, but also reduce surface roughness of workpiece and reduce cutting power consumption.
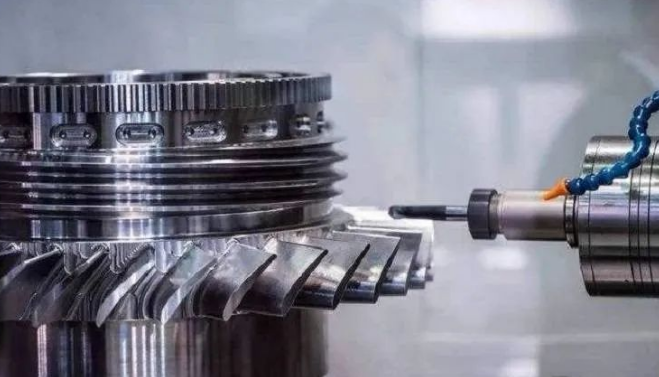
2. Pressure selection of cutting fluid The high pressure scouring of the cutting fluid plays a role in chip breaking and chip washing in part machining. In some hole machining occasions, especially deep hole machining, the pressure of the cutting fluid has a vital impact on the surface quality and tool life. When selecting cutting fluid, the cost of the machine tool should be considered comprehensively. The higher the cutting fluid pressure, the higher the configuration requirements of the machine tool, and the higher the overall cost. The cooling system of the machine tool is composed of cooling water tank, filter, pump (high pressure and low pressure), water pipe, nozzle, seal, etc., to improve the cutting fluid pressure, and relevant connecting components need to be matched with high pressure components. General CNC machine tools are equipped with common chip punching cooling system, and central cooling system is selected when processing requirements are high. The cutting fluid required for common chip cleaning can select small pressure and large flow parameters to move the cutting belt in time and take away the chips attached to the workpiece, guard plate and fixture. Generally, the pressure parameter is 0.04~0.06MPa for common chip cleaning cooling. High-pressure pump is selected for the central cooling system. High-pressure cutting fluid passes through the center of the main shaft, then passes through the tool body, and is directly sprayed to the cutting position of the tool. High-pressure water flow is used to break the chips, and the chips in the narrow space are forcefully washed out, thus playing the role of chip breaking, cooling, lubrication, and chip washing. According to the selection of pressure, the central cooling system can be divided into four grades: low pressure, medium pressure, high pressure and ultra-high pressure.
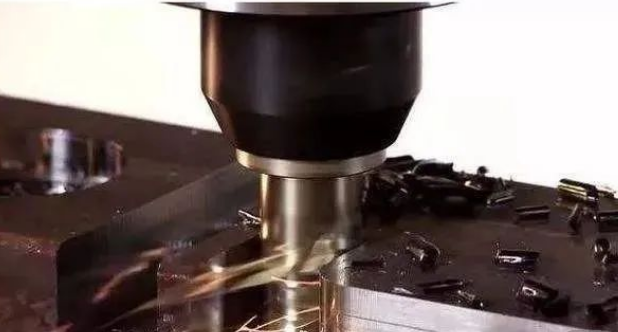
3. Selection of cutting fluid flow The scouring action of the cutting fluid washes the remaining chips on the workpiece, cleans and cleans the fixture, and takes away the cutting heat. Generally speaking, the larger the flow rate of cutting fluid, the more obvious the chip cleaning effect and the better the cooling effect. However, the larger the flow rate, the larger the capacity of the water tank required to store the cutting fluid, and the corresponding increase in the manufacturing cost and equipment floor area. Therefore, the flow rate of cutting fluid is not the greater the better, but the smaller the better under the conditions of meeting the working conditions, so as to reduce the total cost. In order to facilitate heat dissipation and supply sufficient cutting fluid, the capacity of the water tank should be 3-5 times of the flow of the cooling pump of the system.
Selection of emulsion in various working conditions of aluminum alloy processing Emulsion is mainly used for cooling, lubricating and chip cleaning in processing. Compared with most steel and cast iron materials, aluminum alloy has an obvious advantage: lower yield strength. Its flexibility will cause two serious problems: First, it is easy to bond. The aluminum particles bond to the surface of the cutting tool, seriously affecting the surface roughness of the workpiece, or forming a "bonded" chip accumulation on the tool, thus forming a bad cutting trace. Second, due to the high ductility of aluminum, it may form long strip cracks, making the cutting process difficult, and the cutting debris is difficult to be taken away by the cutting fluid. 1. Selection principle of rough and finish machining During rough machining, the machining allowance and cutting amount are large, resulting in a large amount of cutting heat and severe friction, which can easily lead to rapid wear of the tool. The purpose of using cutting fluid is to reduce the temperature of the cutting area. It is advisable to select the cutting fluid with the main cooling property, such as water-soluble synthetic cutting fluid or low-concentration emulsion. During finishing, the main function of cutting fluid is to improve the machining accuracy of the workpiece and reduce the surface roughness. At this time, the cutting fluid with good lubrication and cooling performance should be selected. 2. Selection of cutting fluid when using different processing methods During face milling, the cutting speed is fast, the cutting amount of the tool is large, and the cutting chips are large. The cutting chips should be washed away in time to avoid scratching the machined surface. This is the biggest problem facing the milling process, and large flow of cutting fluid should be used for washing. During hole machining, it is difficult to remove chips. The friction between the tool, workpiece and chips will generate a large amount of heat, which can not be transferred in time, resulting in tool burns and serious damage to the surface roughness of the workpiece. In order to solve this problem, in addition to reasonably selecting the geometric angle of the tool to ensure chip separation, chip breaking and chip removal, the selection of cutting fluid is the key. At this time, the cutting fluid with good cooling, lubrication and cleaning performance should be selected, such as extreme pressure emulsion.