The industrial reducer plays the role of matching the rotational speed and transmitting the torque between the prime mover and the actuator. It is a deceleration transmission device and is widely used in mechanical equipment. 01 Installation points of the reducer The installation of the reducer is a delicate and complicated work with high technical requirements, and the operation rules and design data must be strictly followed during the operation. The general installation sequence is: leveling and alignment of the equipment, cleaning and assembling, adjustment and trial operation. (1) Before installation and use, the installation shaft of the reducer should be cleaned, and the installation shaft should be checked for bumps and dirt. When the reducer is installed obliquely, it should be ensured that the highest gear shaft bearing is lubricated by the Gear Oil in the box, and that the gas in the box can be discharged from the highest position of the box. (2) When the industrial reducer is assembled with the actuator and the prime mover, the connecting flange should be cleaned and polished to ensure the flatness of the straight mouth of the butt joint of the connecting flange to ensure that it is flush, and all bolts around the flange should be aligned and tightened. (3) The assembled transmission elements (couplings, sprockets) should be kept in rotational balance to avoid impermissible radial or axial forces. Usually, the assembly fixture and the inner thread of the shaft end are used to press the transmission parts with bolts, otherwise it may cause damage to the internal parts of the reducer. (4) The installation of the reducer must be rigidly fixed on a solid horizontal foundation or vertical frame, and be leveled. It is necessary to ensure that the coaxiality of the prime mover, coupling, reducer and actuator is consistent to avoid damage caused by additional stress on the input, output shaft and bearings of the equipment due to running deflection. The coaxiality of the two connected shaft extensions should be controlled within the range of φ0.1mm, and a gap of 2-8mm should be left between the end faces of the two shaft extensions. The size of the gap should be determined according to the specific conditions of the equipment connected to the reducer. It is necessary to ensure that the reducer bearing is not subject to additional axial force. In order to avoid the deflection of the main shaft of the working machine and the additional force on the bearing of the reducer, the distance between the reducer and the working machine should be as small as possible without affecting the normal work, and its value is 5-10mm. (5) Filling gear oil: The oil level should choose the recommended value of the reducer, or use the oil that is completely equivalent to the recommended oil. And the amount of oil should be correct, each reducer has a label indicating the level and quantity of the recommended oil. The oil mirror is a display mirror for the oil level of the reducer. On one side of the reducer, the oil level should reach the upper and lower positions of the middle of the oil mirror when filling oil. Importance of the correct amount of oil: In splash-lubricated gearheads, the correct amount of oil is especially important when the load is close to thermal power. In some cases just because 15% more oil is added, the operating temperature may rise to 15-20°C above the normal temperature, which will reduce the lubricating ability of the oil and cause serious damage to the reducer. When the oil level is lower than the oil level indicated by the logo, the gears may not get oil, making splash lubrication impossible. 02 Common fault analysis Due to the harsh operating environment of industrial reducers, failures such as wear and leakage often occur, which are manifested in the following aspects: (1) The bearing chamber of the reducer is worn. It also includes the wear of the housing bearing box, the bearing chamber of the inner hole of the box, and the bearing chamber of the gearbox. This situation occurs mainly due to improper adjustment of the parallelism and coaxiality of each shaft when installing the shaft and bearing, and the deflection force (radial or axial) or abnormal vibration of the box occurs during long-term operation, resulting in the shaft. And the bearing force will cause certain wear on the bearing chamber. (2) The shaft diameter of the gear shaft of the reducer is worn. The main wear parts are the shaft head, keyway, etc. The reason for this kind of failure is the frequent overload start and the material problem of some parts during the operation.
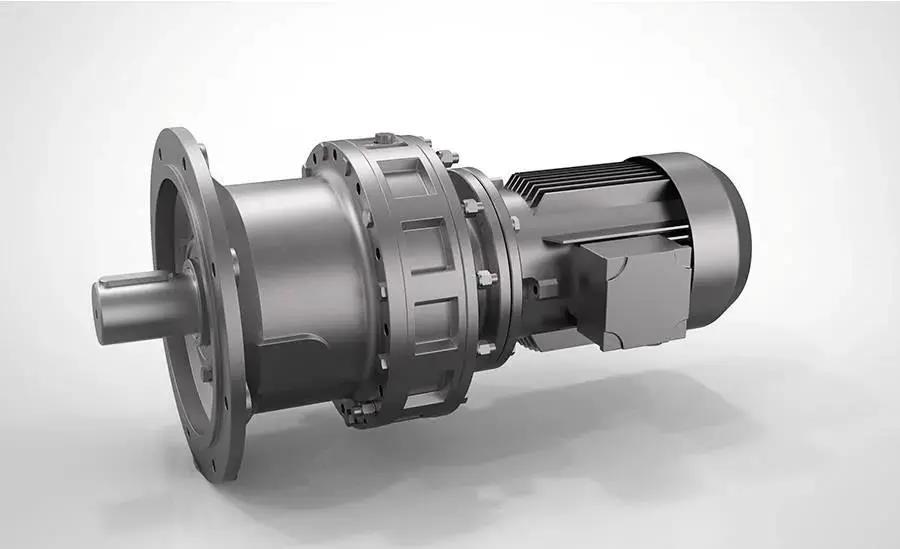
(3) The bearing position of the drive shaft of the reducer is worn or the bearing is faulty. Incorrect assembly will not only accelerate the wear of the bearing, but also cause failures such as fracture and high temperature seizure. Especially for the type of bearings that cannot be self-aligned, when the journal or bearing seat hole has poor machining accuracy or improper installation, and the deflection of the shaft is too large, the inner and outer rings of the bearing will be inclined to each other, resulting in uneven distribution of the bearing workload. Pressure concentrations will fail prematurely. (4) The joint surface of the reducer is leaking. It is manifested in the leakage of oil at the joint surface of the reducer case and the bearing end cover, mainly due to the leakage of the joint surface sealing gasket or the application process of the sealing compound; improper maintenance process, when the equipment is overhauled, due to the removal of dirt on the joint surface Incomplete, or improper selection of sealant, reverse installation of seals, and failure to replace seals in time will cause oil leakage, which can be avoided after strengthening the assembly process requirements. (5) The gear teeth of the reducer are invalid. Common gear tooth failure forms are: tooth breakage and tooth surface damage. The fracture of gear teeth generally occurs at the root of the tooth, because the bending stress at the root of the tooth is the largest and there is stress concentration. The damage of tooth surface can be divided into fatigue pitting corrosion, abrasive wear, gluing and plastic deformation of tooth surface. Measures to prevent gear tooth failure include: increasing the hardness and surface roughness of the tooth surface; selecting lubricants with higher viscosity; supplying enough lubricating oil and keeping the lubricating oil clean; avoiding frequent startup and severe overload and impact; improving assembly Quality, strengthen maintenance management. 03 Maintenance and Assembly Considerations Whether the gear meshing of the industrial reducer meets the requirements, whether the contact surface is good, and whether the assembly clearance of each part of the bearing part is good, is a sign of the quality of the gear assembly and repair of the reducer. (1) When inspecting the gears, if uneven wear, traces or partial peeling of the tooth surfaces are found, the center distance of the gears, the non-parallelism of each shaft, the meshing clearance of the gears, the levelness, coaxiality and Contact situation, lubricating oil quality, whether there are other metal or non-metal objects falling into the reducer, and whether the gear keys and nuts are loose, etc. Problems detected must be dealt with in a timely manner, and must not be forced to operate. (2) During the inspection, if a certain tooth surface is found to be peeling off, its area does not exceed 30% of the effective combined area of the gear. When other parts are normal, they can continue to be used, but it is necessary to regularly check whether there is any change. When the tooth surface spalling continues to increase and the operating state gradually deteriorates, it should be replaced immediately. (3) When it is found that the wear degree of the two gears is very different and cannot be used together, only replacing the pinion is a temporary measure, and it should be replaced in pairs as much as possible. In addition to repairing or replacing the reducer, shaft and gear, it is also necessary to replace the worn or damaged rolling bearing or sliding bearing bush for inspection, adjust the clearance, clean the box and the parts installed in the box, and replace the lubricating oil. (4) After cleaning the reducer, be sure to tighten the plug of the oil drain hole, and add enough lubricating oil according to the required lubricating oil grade. When overhauling the reducer, prevent foreign objects from falling into the box. (5) The quality of the seal at the joint surface of the upper and lower casings of the reducer is the key to preventing oil leakage. Generally, the connection between the reducer box body and the box cover or flange can be sealed with gaskets or glue. Gasket materials include cardboard, copper sheet, lead sheet, oil-resistant rubber, etc. When the contact area to be sealed is large and the joint surface is rough, the thickness of the gasket should be increased, and the gasket must be pressed tightly when installing.