No matter how good the heat transfer oil is, there will be many problems if it is used improperly. These points must be paid attention to! 1. Precautions for the operation of heat transfer oil 1) Initial installation Consider flushing the system (to eliminate contaminants and water) before commissioning. Before filling the new system, all safety and control devices are in working condition, and the system has undergone a leak pressure test. Do not use water during the test because it is difficult to remove the water from the system. Use internal pressurized air and soapy water on the outside of all joints or use oil in the system to test for leaks. Use a vacuum pump to extract air and fill the system from the expansion tank. The fluid should circulate in the system for three to four hours to eliminate air bubbles and ensure that the system is full. When the system is cold, the expansion tank should be at 25% oil level. 2) Start The temperature should rise slowly while allowing the full flow of heat transfer oil to circulate. Air and water must be allowed to leave the system. 3 Routine operation In order to prevent hot spots, the circulating pump must always be in operation, and the heat transfer oil will flow through the heater before starting. To prevent the stored heat from forming damaging hot spots, the heater must be turned off before the pump so that the heat transfer oil can circulate and dissipate heat. The system should be checked regularly to ensure that it is operating within the design parameters, and to check for hot spots and leaks.
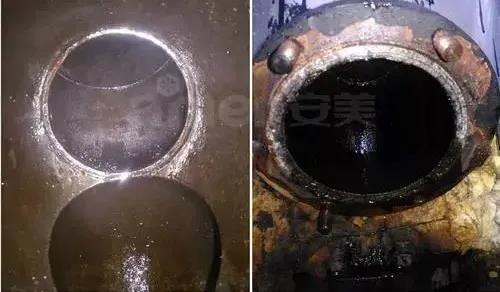
2. System Maintenance When the system is maintained, the heat transfer oil should be kept flowing to prevent the sediment from falling off and starting problems. Leaks or spills must be dealt with immediately. Depending on system conditions, it may be desirable to flush the boiler circuit during each shutdown. If any pipeline or equipment insulation layer is found to be soaked by oil, it should be removed and replaced in time with a clean, oil-free insulation layer, and the cause of the leakage should be corrected. 1) Water pollution The water in the heat transfer system may pose a safety hazard and threat to the equipment. Water detection: Attention must be paid to sudden changes in the monitoring system; whether it is pump cavitation, expansion tank volume increase, abnormal sound or pressure increase, especially during start-up. All of these can indicate that there is water in the system. Best method of operation: Do not pressure test the new system with water. If you want to replace the system components, if they have been hydrostatically tested, make sure to dry them thoroughly before installation Heat transfer oil must not be stored outdoors. 2) System cleaning Pay attention to when cleaning the system: If ignored, effective heat transfer system cleaning will be very challenging. In most cases, detergent products are required to dissolve the accumulated soft deposits. For very dirty systems, corrosive cleaners (used by professional contractors) may be the only way to remove hard deposits. Since it is impossible to completely drain all lines and low points, the flushing fluid will remain in the system. Therefore, avoid using products such as heating oil and solvents for washing, because the residues of these products will evaporate during operation and become a fire hazard. Likewise, chemicals or water-based cleaners can contaminate the system. The steam may rupture the system pipes. The preferred flushing product is mineral oil. If you suspect that the system is dirty, you can use detergent products. The flushing medium should be circulated in a hot state above 85°C (185°F) for at least 48 hours, and then discharged when it is still hot. Increasing the system temperature can reduce the duration and effectiveness of the flush. It's worth noting that rinsing with system cleaner for 24 hours at 55°C (130°F) can be reduced to about 2 hours at 150°C (300°F). The flushing speed is also important and should be kept turbulent. 3) System flushing When debugging the heat transfer system, it is recommended to flush the system to ensure that all debris (sealing materials, metal particles, etc.) or cleaning agents are removed before the system is put into operation. It is recommended to flush with the same heat transfer oil that will be used during operation. According to the needs and suitability of the site, if the analysis of the heat transfer oil after flushing is satisfactory, you can reuse this part of the heat transfer oil as the system oil. During the flushing process, the heat transfer oil should be circulated for at least 24 hours. During the flushing process, the condition of the filter should be monitored and replaced as needed. At least the filter should be replaced when the final heat transfer oil filling in the system is completed. The filter level selected for flushing should be suitable for the level used during normal operation. For example, if a 100 micron filter is used during normal operation, the filtration level should be reduced from 100 microns to 25 to 10 microns during flushing. 4) Supplement of heat transfer oil Heat transfer oil can be added as a supplement to the inlet of the expansion tank or pump. Do not add ordinary oil to the system containing heat transfer oil. The thermal stability of heat transfer oil will decrease proportionally with the addition of conventional oil. 5) Safety precautions Fire protection, in order for the heat transfer oil to ignite, many conditions must be met at the same time: the heat transfer oil must reach its flash point, the system must leak, steam can escape, and there must be an ignition source close enough to the leak point to ensure sufficient vapor concentration High to ignite. Reduce the possibility of fire: The best heat transfer fluid conditions must be maintained. The heat transfer system should be located in a well-ventilated area. The heat transfer system must be maintained to prevent leaks and malfunctions. The soiled insulation material should be replaced as soon as possible. During shutdown, the system should be thoroughly inspected for signs of leakage. The flow between heaters must be maintained to minimize fluid overheating. Insulation: It is recommended to use closed-cell insulation instead of open-cell insulation. Dirty insulation materials should be replaced as soon as possible to avoid flow loss, major leaks, and heater tube rupture Toxicity Generally speaking, a good heat transfer oil is formulated with solvent refined or hydrotreated lubricating oil. According to existing toxicological information, these products will not cause significant adverse health effects when handled and used correctly. In addition to paying attention to good personal hygiene, it is not recommended to take special precautions, including avoiding repeated skin contact.