How can we simply judge the performance and quality difference of different cutting fluids in daily use? Even if we are in the factory, we can compare the main performance indicators of different cutting fluid products in the simplest way. You only need to spend 5 minutes, which may save at least 10% of the cost!
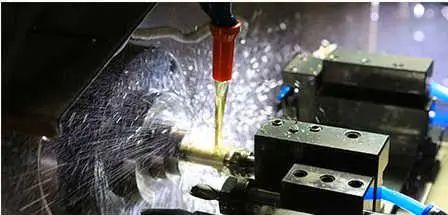
1) Cutting fluid performance The longer the tool life and the better the surface finish, the better the cutting fluid lubrication performance. In the case of the same equipment, the same tool and processing the same workpiece, compare the tool life (number of parts that can be processed by a single tool or cutting distance) and processing quality (surface finish). Lubrication performance is a very important index of cutting fluid. It directly affects the processing quality and cost. However, it is impossible to judge intuitively, because you cannot know the formula of cutting fluid and the effective lubricating composition. 2) Stability Delamination, impurities and non-uniformity are found in any of the following two items. It can be determined that the cutting fluid has poor stability. ①. Take a proper amount of stock solution and place it in a transparent container for 24 hours to observe whether the stock solution has layers and impurities and is uniform; ②. Take an appropriate amount of the original solution, prepare a 5% diluent with tap water, leave it in a transparent container for 15 minutes, and observe whether the diluent is uniform and whether there are layers and impurities. 3) Defoaming property Through the experiment, foam can disappear in 15 seconds, and foam performance is qualified. The faster the defoaming speed, the better. Prepare 5% diluted solution and place it in a transparent reagent bottle, with the lid closed. Then shake the reagent bottle up and down with normal force for 15 seconds, then stand on the table to start timing and observe: if the foam generated in the bottle can disappear within 15 seconds, the foam performance is qualified. 4) Rust and corrosion prevention The later the corrosion occurs, the stronger the natural anti rust and anti-corrosion ability. A proper amount of 5% diluted solution shall be prepared. Machined parts (with machined surfaces) of moderate size shall be soaked in the cutting fluid for an appropriate period of time (half an hour to several hours, depending on the length of part processing time), and then taken out. After 3-5 days of observation in the air, the parts will rust or corrode. In particular, this method can only be used to judge the performance. For some special materials (such as aviation aluminum alloy), more strict laboratory verification is often required. 5) Antibacterial ability The earlier the cutting fluid becomes odorous, the worse its antibacterial ability is. Prepare an appropriate amount of 5% diluent and keep it in the container, sniff the change of cutting fluid smell regularly. This item is directly related to the service life of cutting fluid. The principle of inhibiting bacteria of most products depends on the bactericide in the product formula, and only a few products use biological bacteriostasis. 6) Resistance to waste oil Observe the change of the dividing line: the cutting fluid with weak anti impurity oil ability will soon mix with the oil to make the dividing line more and more vague. Prepare an appropriate amount of 5% diluent and let it stand in a transparent container, then drop an appropriate amount of hydraulic oil or guide rail oil into the cutting fluid. The oil will float on the surface of the cutting fluid, and there will be a clear boundary between oil and water. 7) Nitrite content Use a special nitrite test paper to test. Or ask the manufacturer to provide MSDS documents If the test paper turns red, it can be determined that it contains carcinogenic nitrite in 99% of cases. The deeper the redness, the higher the content. 8) Consumption of cutting fluid Two reagent bottles can be used to prepare diluents of the same concentration and maintain the same volume. Then take two identical standard samples (such as two long steel bars), dip the samples into the cutting fluid in the reagent bottle in the same way and take it out (the cutting fluid will adhere to the samples and drip on the outside). After repeating the same immersion and withdrawal action for the same number of times, compare the amount of cutting fluid remaining in the reagent bottle. Too much remains, indicating that this cutting fluid is not easy to be consumed by parts and chips. Taking away products with large consumption will bring higher use costs. In addition, there is a lack of simple methods to compare the cooling performance of cutting fluids. However, as long as the product is water-soluble, the cooling performance is similar. For fully synthetic grinding fluid, there is also the requirement of sedimentation. That is, the ability of wear debris and metal particles to settle rapidly in the grinding fluid. This can directly observe the change of the transparency of grinding fluid. Products with good sedimentation can maintain good transparency for a long time.
Even in general factories, without professional testing tools, using the above simple methods can obtain more intuitive and effective results.