To ensure the safe and stable operation of aviation engines, it is necessary to use a lubrication system to provide a stable flow of lubricating oil to various lubrication parts of the engine. The development of aviation engine lubrication systems and aviation lubricants has gone through two stages. Before the 1980s, traditional lubrication systems were basically used in aviation engines, and then a new generation of aviation engine lubrication systems began to be used. The working mode of the new generation lubrication system requires a continuous cycle of heat absorption, heating up, oxidation, and cooling. It is necessary to use a new generation of aviation lubricating oil to meet the demanding working needs of aviation lubrication systems. In this way, aviation engines and aviation lubricants have been constantly updated and replaced! Development History Due to the relatively low requirements for operating temperature and load in early engines, the main requirement for lubricating oil was low-temperature starting performance. Therefore, mineral oils with low kinematic viscosity (2-9 mm2/s, commonly 20-25 mm2/s for piston engines) and easy to refine were the most common lubricants at that time.
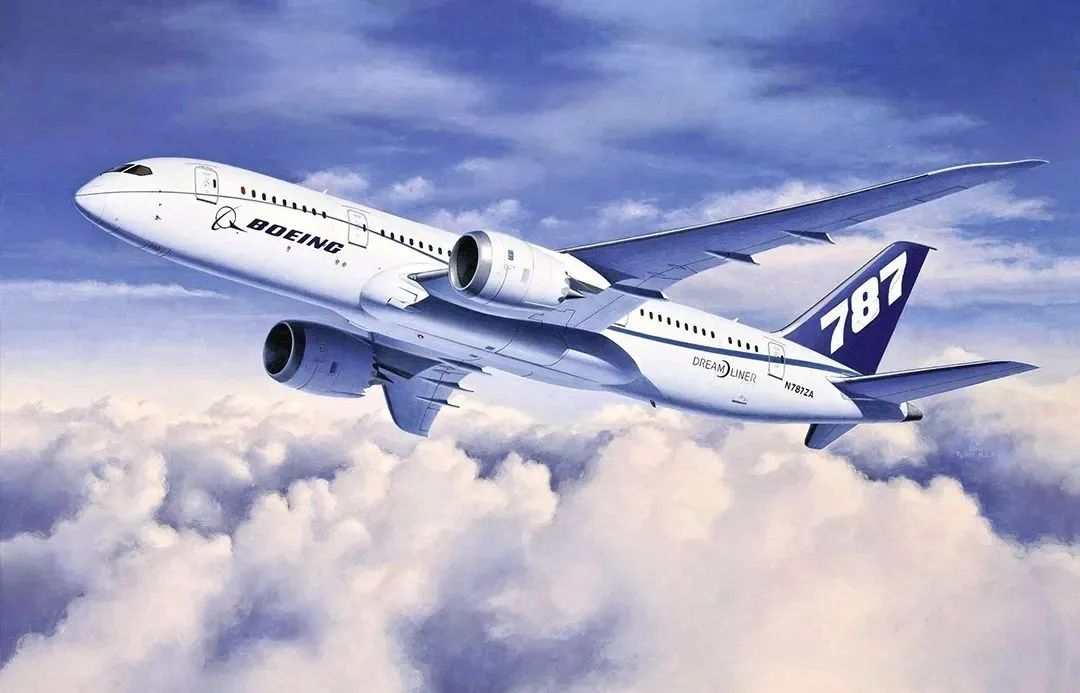
In the 1950s, gas turbine engines developed rapidly, and turbofan engines with greater thrust and higher bypass ratios began to enter the application stage. Lubricating oils based on mineral base oils are prone to volatilization and thermal degradation at higher temperatures, hence the application of lubricants synthesized from natural organic compounds. Synthetic oil exhibits excellent performance and is very suitable as a Base Oil, but its viscosity is generally only 3 mm2/s, lacking sufficient load-bearing capacity. After adding a thickener (composite ester), the viscosity of synthetic oil can be increased to about 7.5 mm2/s at 100 ℃, providing the required load-bearing capacity. In addition, unlike mineral oils, synthetic oils must rely on additives to improve their antioxidant and thermal degradation resistance, which is crucial for ensuring the cleanliness of the engine after long-term operation. At the same time, the US military standard MIL-L-7808 (later renamed MIL-PRF-7808) and the UK Department of Defense standard DERD 2487 (later renamed DEF STAN 91-98) emerged, corresponding to the mainstream viscosity requirements of 3mm2/s and 7.5mm2/s, respectively. Among them, the viscosity standard of 3 mm2/s is still applied so far. For example, the auxiliary power unit (APU) of Boeing 787 Dreamliner (below) only approves the use of 3 mm2/s lubricating oil, because 3 mm2/s lubricating oil has low temperature flow characteristics, which helps APU start at low temperature.
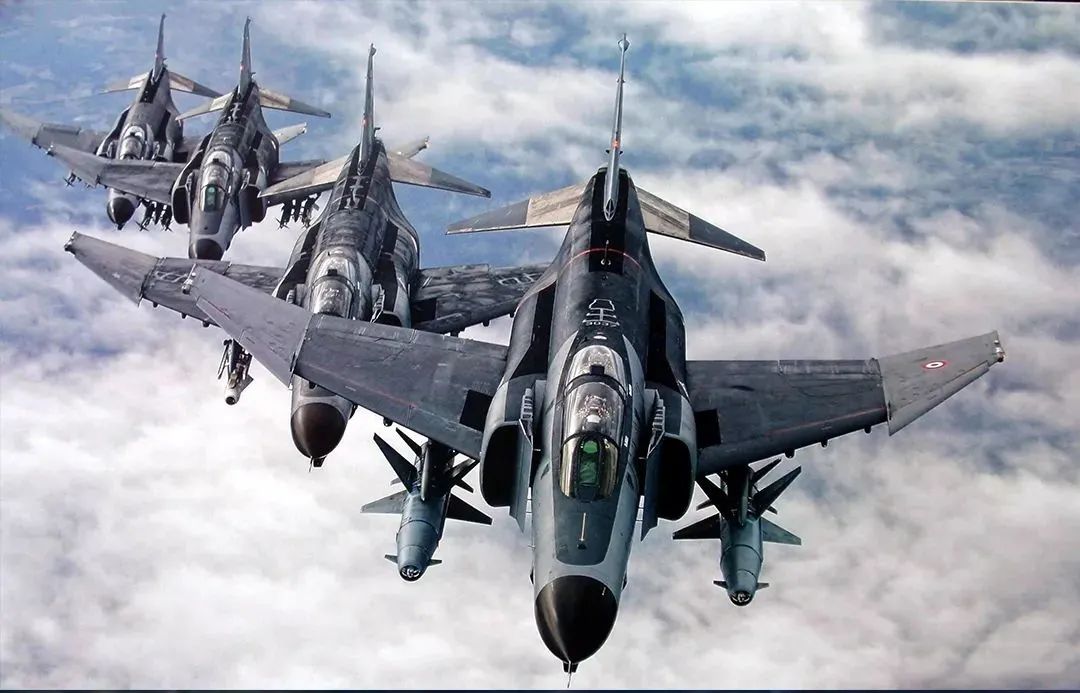
In the 1960s, with the continuous increase in engine size and power output, there was a demand for the thermal stability and high load-bearing capacity of lubricants. The United States developed the US military standard MIL-L-23699 (later renamed MIL-PRF-23699) for the second generation of lubricants based on "hindered esters" with a viscosity of 5mm2/s.
The second generation of lubricants was first used in engines in the United States and later widely used in engines in the UK, Canada, and France. (Second generation fighter jet shown below)
Working characteristics
The working process of the aviation gas turbine engine lubricating oil system is shown in the following figure. The lubricating oil is stored in the oil tank. During engine operation, the oil pump provides continuous pressure and sends the lubricating oil pump to the bearing chamber, accessory gearbox, and its transmission device through the oil supply pipeline.
Large and medium-sized aircraft engines usually use pneumatic seals to seal the bearing cavity, so the return oil pipe from the bearing cavity is usually a mixture of lubricating oil and air mist. The temperature of the rotor bearings in front of the combustion chamber (compressor part) is lower than that of the rotor bearings behind the combustion chamber (turbine part), so the working temperature difference of the lubricating oil in these bearing cavities can reach 100 ℃. After the lubrication task is completed, the oil gas mixture and the lubricating oil discharged from the accessory gearbox are pumped to the heat exchange equipment for cooling, then the oil gas is separated, and finally returned to the oil tank for the next cycle. The lubricating oil system can complete a maximum of three cycles per minute. When the engine stops and the oil pump stops working, the heat in the lubricating oil cannot be released actively, but increases the possibility of oxidation and carbonization through the Free cooling process. From the above, it can be seen that the operation of aviation engine lubricating oil has the following characteristics: lubricating different types of components at different temperatures (including bearings and gears); The temperature of lubricating oil constantly changes during pipeline circulation; Most of the time coexists with hot air; Contact different types of materials (including metal and elastic seals, etc.). These characteristics have high requirements for the thermal stability, antioxidant capacity, compatibility, and load capacity of lubricating oils.. Development direction In order for the aircraft to continue flying for longer periods of time and over longer distances, it is necessary to improve the engine's propulsion efficiency and thermal efficiency, which resulted in the engine operating temperature being much higher than in the 1960s. Except for operating at higher temperatures, lubricating oil is generally not completely replaced before engine maintenance. Currently, the service life of engine oil is further extended, which means that lubricating oil needs to maintain normal operation within longer maintenance intervals. Therefore, it is more important to avoid coking of lubricating oil and improve compatibility with elastic seals. Avoid coking Coking refers to unnecessary carbon buildup during engine operation. When engine lubricating oil is exposed to high temperatures, carbon deposits will gradually form. After running the engine for a period of time, there are several common coking phenomena (as shown in the following figure):
One is film coking, where the carbon layer adheres to a smooth metal surface and curls or falls off, usually occurring during engine cycling; The second is gas phase coking, which can be seen in the residual oil ports or vents in the hot parts of the engine. These areas are usually smooth matte surfaces, and with a high mixing ratio of air and oil, the surface will appear rough after coking; The third is agglomeration or pit like carbon deposition, which can be seen in places where lubricating oil accumulates and forms thick blocks. This type of coking may be related to the normal stopping of the engine. When parking, the oil stops flowing and cannot be dissipated through the heat exchanger, but the heat is absorbed and oxidized by the oil; The fourth is dynamic coking, which forms an irregular flow zone in the lubricating oil pipeline due to carbon deposition, which is one of the possible mechanisms leading to blockage of the oil supply and return pipelines. At present, some aircraft operators still believe that coking is a normal phenomenon for engine lubricating oil to work in high-temperature environments. But if preventive measures are not taken to coking the lubricating oil, it will cause additional costs and potential safety impacts on engine maintenance. For example, coking can clog the return, exhaust, and supply pipes of the oil filter and lubricating oil system, resulting in insufficient lubricating oil flow and pressure, or forcing lubricating oil into engine areas that should not be entered, and even leading to bearing failure or engine fire. In fact, using lubricants with strong thermal stability can improve coking conditions, effectively reduce or avoid the additional work of engine cleaning carbon or replacing polluted engine components. It is one of the effective ways to improve engine maintenance efficiency, reduce maintenance costs, and improve safety. Improve compatibility with elastic seals The commonly used sealing material for engines and their components is fluororubber A/B/E. In order to make the seal effective, the seal will absorb some lubricating oil expansion, thereby playing a sealing role. Based on experience, the optimal amount of lubricating oil absorption should allow the seal to expand by 12% to 20%. If the compatibility between lubricating oil and sealing components is not ideal, it can lead to deterioration of the sealing components, causing excessive expansion or contraction of the sealing components, leading to lubricating oil leakage or other foreign objects polluting the lubricating oil system. Generally speaking, engine lubricating oil is mainly based on synthetic polyol esters with alcohols and fatty acids as the basic raw materials, rather than mineral base oils. Compared with mineral base oil, other components of synthetic oil mainly include additives that provide the required performance requirements, including dispersants to keep the engine clean, surface active additives (including wear-resistant components) to reduce metal to metal contact wear, corrosion inhibitors, and antioxidants that help protect the base oil from thermal degradation and coking. However, antioxidants in some high thermal stability lubricating oils can lead to deterioration of elastic seals and leakage due to malfunctions. For example, CFM56 from CFM International and CF34 from General Electric use high thermal stability lubricants with inappropriate antioxidants, leading to deterioration of elastic seals, forcing airlines to conduct additional regular inspections or modify corresponding seals to avoid oil leakage. How to maintain high thermal stability while making lubricating oil more compatible with elastic seals, thereby saving costs and improving safety margins, is an important direction for the development of aviation engine lubricating oil.
After decades of development and accumulation, the high thermal stability specifications and high performance level specifications represented by the US military standards MIL-PRF-23699G and SAE AS5780D stand out for their advantages in preventing lubricating oil coking and improving the compatibility of elastic seals. These standard aviation lubricants and aviation materials technology can provide you with them.
In addition, Aviation Materials Technology will also be committed to the development of high thermal stability or high-performance grade aviation engine lubricants, which will be the future development direction of aviation lubricants.