1. The main performance indicators of grease ①Dropping point: refers to the temperature at which a certain fluidity is reached when heated under specified conditions. It can generally determine the operating temperature of the lubricating finger (the dropping point is 15-30 degrees higher than the operating temperature). ② Cone penetration: refers to the depth (unit: 1/10mm) of the test cone penetrating freely and vertically into the grease within 5s under the specified temperature and load. It is a measure of lubricity and hardness. ③ Colloidal stability (oil separation): refers to the ability of the lubricating finger to preserve oil in the skeleton of its thickener under the action of external force, which is determined by the amount of oil. When the oil separation of the grease exceeds 5%-20%, this grease can basically not be used. ④ Oxidative stability: refers to the ability to resist oxidation during storage and use. ⑤ Mechanical stability: refers to the ability to resist consistency changes under mechanical working conditions. Poor mechanical stability, it is easy to cause the consistency of the grease to decrease. ⑥ Evaporation loss: refers to the percentage of the total loss under specified conditions. It is an important factor affecting the service life of grease. ⑦ Water resistance: refers to the ability to be insoluble in water, not absorb water from the surrounding medium, and not be washed away by water. ⑧ Similar viscosity: refers to the ratio of shear stress to shear velocity when non-Newtonian fluid flows. When the rotational speed is high, the viscosity is low, and vice versa.
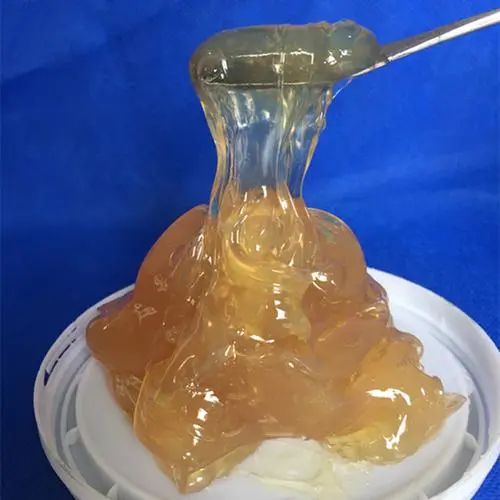
2. Failure analysis of lubricating grease ①Failure caused by physical factors In use, the grease will be subjected to mechanical shearing and centrifugal force at the same time. Under the action of mechanical shearing and centrifugal force, the grease will be thrown out of the friction interface to separate oil, resulting in the reduction of grease oil content and the reduction of cone penetration and hardening. It will fail completely; under the action of mechanical shearing, the structure of the grease will be destroyed (such as the disengagement or orientation of soap fibers), which will cause its softening, decrease in consistency and increase in oil separation, etc., and eventually lead to failure. Under normal circumstances, when the transmission speed of grease is increased by 2000r/min, its life will be reduced by about half. Under high shear stress, the speed is doubled, and the service life is only 1/10 of the original life. ② Failure caused by chemical factors The grease reacts chemically with oxygen in the air to produce acidic substances. It first consumes the antioxidant additives in the grease, but after a certain level, the generated organic acid will corrode the metal components and destroy the structure of the grease, making it drop point. decrease, Base Oil viscosity increases, and fluidity deteriorates. A large number of tests have shown that the higher the temperature, the more obvious the decline in the life of the grease. For example, when the temperature is between 90 and 100 degrees, the life of the grease will be reduced by about half for every 19 degrees of temperature increase, and at 10 to 150 degrees, every 15 degrees of temperature increase, the life of the grease will also decrease by half. In addition, moisture, dust, and harmful gases in the environment in which the grease is used are also important factors for its deterioration. For example, the abrasive particles such as copper, iron, lead and bronze are mixed into the grease, which will catalyze the oxidation of the grease. In short, there are many reasons for the failure of lubricating grease, which may sometimes be caused by a certain reason, but it is more the result of the simultaneous action of multiple factors, or one reason is the breakthrough, and then other reasons work together.
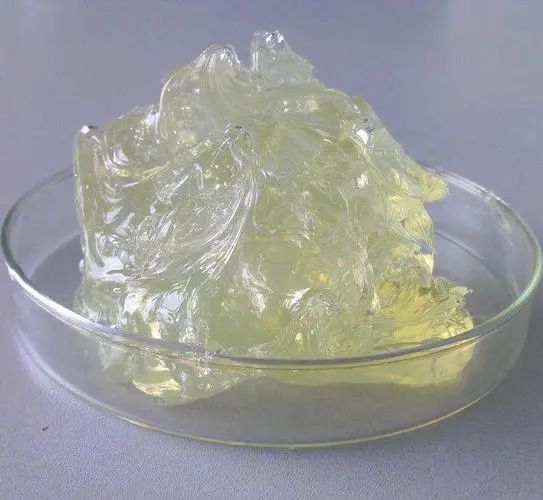
3. Reasonable selection of lubricating grease When selecting grease, the working conditions of the friction pair (load, speed, temperature), working state (continuous operation, intermittent operation, vibration and shock, etc.) and working environment (humidity, temperature, air pollution, etc.) should be considered. ). ①The operating temperature of the grease should be at least 20~30 degrees lower than its dropping point When the operating temperature is high, the grease with good oxidation resistance, small evaporation loss and high dropping point should be selected; when the operating temperature is low, the grease with low starting torque and similar viscosity should be selected, such as the grease with synthetic oil as the base oil . ②The selected lubricating grease should be adapted to the use speed of the lubricated friction pair At high speed, a grease with a large penetration degree made of a low-viscosity base oil should be selected; for a low-speed grease, a grease with a high penetration degree made of a high-viscosity base oil should be selected. ③The selected grease should be suitable for the load. For heavy loads, a grease with a high base oil viscosity and high thickener content should be selected. When the load is particularly large, care should be taken to select a grease with extreme pressure additives or fillers (molybdenum disulfide, graphite); when the load is medium and low, the grease with a short structure of No. 2 soap fibers and a medium viscosity base oil is generally used. ④The selected grease should be suitable for the environmental conditions used In the environment where the air is humid or in contact with water, grease with good water resistance such as calcium-based, lithium-based, and complex lithium-based should be selected; when there is a lot of dust, thicker (that is, higher grade) grease should be selected, so that the sealing performance Preferably, impurities can be prevented from being mixed into the friction pair. In the environment of strong chemical medium, synthetic oil grease that is resistant to chemical medium such as fluorocarbon grease should be selected. ⑤The selected grease should be compatible with the grease supply method of the friction pair When it is a centralized grease supply, No. 00~1 grease should be selected; for parts that are regularly filled with grease such as grease guns and grease cups, No. 1~3 grease should be selected; for long-term use without grease replacement, it should be Use No. 2 or No. 3 grease. ⑥ The selected grease should be adapted to the working state of the friction pair For example, when the vibration is large, use grease with high viscosity, good adhesion and vibration damping, such as complex soap-based grease thickened with high-viscosity naphthenic or mixed-base lubricating oil. ⑦The selected grease should be suitable for its purpose of use The grease used for lubrication must be selected according to the type of friction pair, working conditions, working conditions, environmental conditions and grease supply methods; for the grease used for protection, it should be able to effectively protect the metal from corrosion, such as protection For parts in contact with seawater, aluminum-based greases with strong adhesion and water resistance should be selected; general protection greases can be made of solid hydrocarbon-thickened high-viscosity base oils. For sealing grease, attention should be paid to its resistance to the solvent of the medium being sealed. ⑧ The selected lubricating grease should minimize the variety of grease and improve economic benefits. In the case of meeting the requirements, try to use multi-purpose general-purpose greases such as lithium-based grease, complex soap-based grease, and polyurea grease. In this way, the variety of grease is reduced, the management of grease is simplified, and the cost of grease consumption and maintenance costs can be reduced due to the long service life of the multi-effect grease.
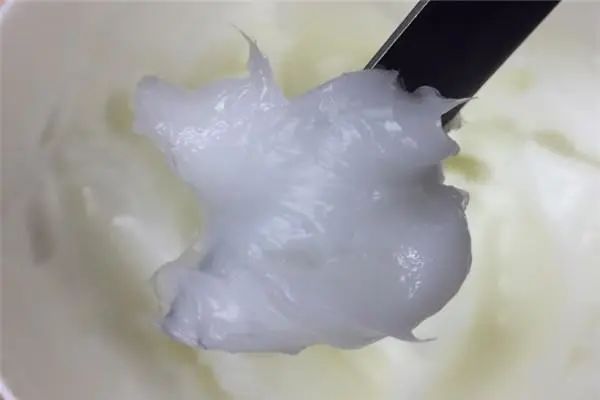
4. The correct use of grease ① The amount of lubrication added should be appropriate If the amount of grease is too large, the friction torque will increase, the temperature will increase, and the grease consumption will increase; while the amount of grease is too small, reliable lubrication cannot be obtained and dry friction occurs. Generally speaking, the suitable amount of grease is 1/3~1/2 of the total void volume in the bearing. However, depending on the situation, sometimes it is necessary to apply grease on the edge of the bearing to implement cavity lubrication. ② Pay attention to prevent the mixing of different types, brands and new and old greases Avoid cross use of grease containers and tools, otherwise, it will have adverse effects such as drop point drop of grease, increase of cone penetration and decrease of mechanical stability. ③ Pay attention to the replacement of new grease Since the variety and quality of grease are constantly improving and changing, when old equipment is replaced with new grease, it should be tested first, and then can be used formally; when replacing new grease, waste grease should be removed first, and parts should be cleaned. clean. When adding grease, the waste grease should be squeezed out until new grease is seen at the grease outlet. ④ Pay attention to the management of the grease filling process Before receiving and refilling grease, strictly pay attention to the cleaning of containers and tools. The grease supply port on the equipment should be wiped clean in advance to prevent the mixing of mechanical impurities, dust and sand. ⑤ Pay attention to the timely replacement of seasonal grease For example, the temperature difference between winter and summer in the environment where the equipment is located varies greatly. If winter grease is used in summer or vice versa, the result will be counterproductive. ⑥ Pay attention to regular replacement of grease The time of adding and replacing the grease should be determined according to the specific use situation, so as to ensure reliable lubrication without causing waste of grease. ⑦Do not pack grease in wooden or paper containers Prevent oil from hardening, mixing with water or being contaminated and deteriorated, and should be stored in a cool and dry place.