With the continuous development of science and technology and the mechanical processing industry, some new and high-performance engineering materials have been widely used. These materials mostly belong to difficult to cut materials with poor machinability, which brings difficulties to cutting processing. In order to solve the machining difficulties of difficult to cut materials, in addition to selecting tool materials, tool geometric parameters, cutting parameters, and mastering cutting conditions such as operating techniques, how to correctly select and use cutting fluids has also become an important link in mechanical machining.
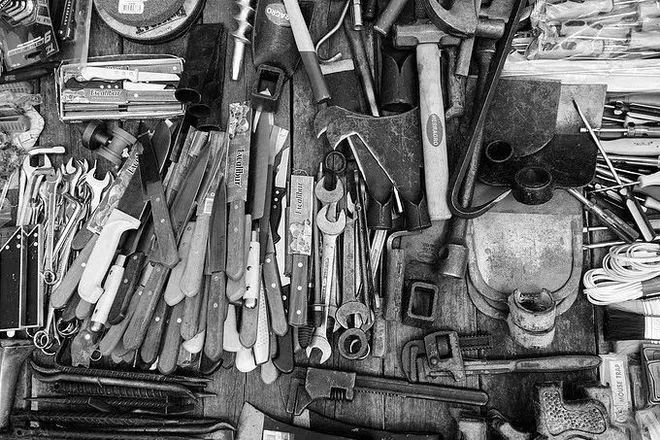
The difference and selection between oil-based cutting fluids and water-based cutting fluids 1. Differences between oil-based cutting fluids and water-based cutting fluids The lubrication performance of oil-based cutting fluid is good, but the cooling effect is poor. Compared with oil-based cutting fluids, water-based cutting fluids have relatively poor lubrication performance and better cooling effect. Slow cutting requires strong lubricity of the cutting fluid. Generally speaking, oil-based cutting fluid is used when the cutting speed is below 30 m/min. Cutting fluids containing extreme pressure additives are effective for cutting any material when the cutting speed does not exceed 60 m/min. During high-speed cutting, due to the large amount of heat generated and the poor heat transfer effect of oil-based cutting fluid, the temperature of the cutting area will be too high, resulting in smoke, fire and other phenomena of cutting fluid. In addition, because the workpiece temperature is too high, thermal deformation will occur, affecting the machining accuracy of the workpiece, so water-based cutting fluid is often used.
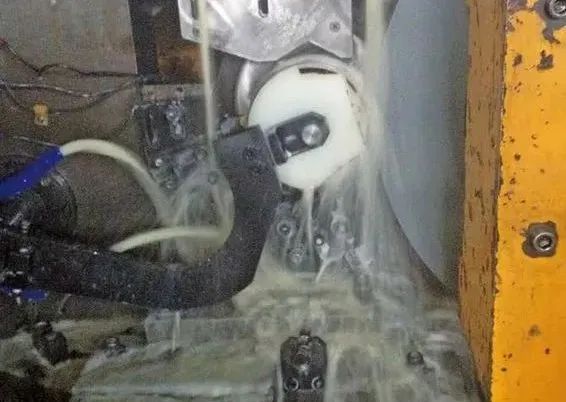
2. Selection conditions of water-based cutting fluid (1) Places with potential fire hazards for oil-based cutting fluids; (2) High speed and high feed cutting make the cutting area exceed high temperatures, with intense smoke and fire hazards; (3) From the perspective of the process flow of the front and back processes, it is required to use water-based cutting fluid in situations; (4) I hope to reduce the pollution and dirtiness around the machine tool caused by oil splashing and oil mist diffusion, in order to maintain a clean operating environment; (5) From a price perspective, for cutting processes with low requirements for easy to machine materials and workpiece surface quality, the use of general water-based cutting fluids can meet usage requirements and significantly reduce cutting fluid costs. 3. Selection conditions of oil-based cutting fluid (1) When the durability of the cutting tool accounts for a significant proportion of the cutting economy (such as high tool prices, difficulty in grinding the cutting edge, long loading and unloading assistance time, etc.); (2) The precision of the machine tool is high, and it is absolutely not allowed to have water mixed in (to avoid corrosion); (3) In situations where the lubrication and cooling systems of machine tools are prone to communication, as well as in situations where there is no waste liquid treatment equipment and conditions available. Maintenance Techniques for Cutting Fluid 1. Maintenance of oil-based cutting fluid The maintenance and management of oil-based cutting fluids is relatively simple, and precautions to be taken include mixing water, chip accumulation, and lubricating oil. The water in oil-based cutting fluid is mixed in from the outside, and a relatively easily overlooked source is the water-based cutting fluid from the previous process brought by the workpiece. When water is contained in cutting fluid, emulsification, corrosion and low lubricity will occur. The water in cutting fluid can be removed by sedimentation separation, filtration and other methods. A large amount of chips, especially some small chips, are easily deposited at the bottom of the oil tank, which can promote the oxidation and deterioration of the oil, produce gelatinous substances, and increase the acid value. Therefore, they should be removed in a timely manner. Many machine tools have oil leakage problems, especially machine tools such as gear hobbing machines, whose structural characteristics make it difficult to avoid the mixing of lubricating oil and cutting fluid. The mixing of lubricating oil will affect the performance of the cutting fluid. When too much lubricating oil is mixed and the cutting performance cannot meet the requirements, additives should be added or the cutting fluid should be replaced. 2. Maintenance of water-based cutting fluid There are two aspects to the maintenance and management of water-based cutting fluids. One is to prevent the mixing and timely removal of external pollutants, and the other is to maintain the stable performance of water-based working fluids, such as concentration, rust resistance, pH value, and antibacterial ability. The concentration of water-based cutting fluid should be controlled within the specified range to ensure that various properties meet the requirements. The concentration can be determined by refraction, oil content of lotion or determination of a specific component (such as base number and alcohol amine content). Determine whether to add water or concentrate after a period of use through concentration measurement.
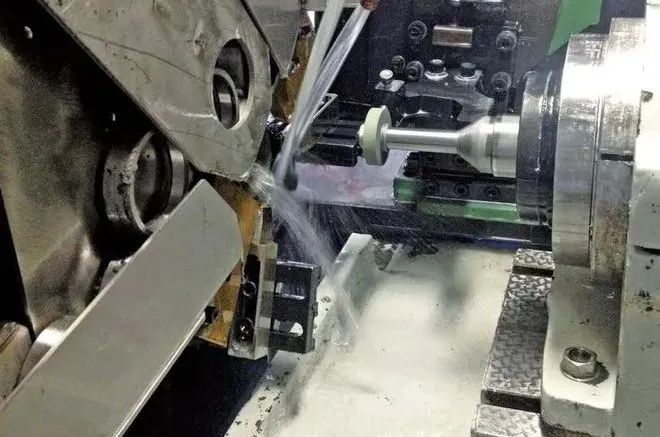
Water-based cutting fluid on the workstation The pH value of water-based liquids usually decreases during use. A decrease in pH value can lead to a decrease in the rust resistance and antibacterial ability of the cutting fluid. If the concentration meets the requirements and the pH value cannot reach the specified value, triethanolamine or other substances should be used in a timely manner to increase the pH value of the working fluid and control it within the specified range. The reasons for the decrease in rust resistance include consumption of rust inhibitors, decreased pH, bacterial growth, and low working fluid concentration, which need to be addressed specifically. If there is excessive consumption of rust inhibitors, they can also be added to the working fluid. Proper maintenance and management of water-based cutting fluid during use can not only achieve the best cutting effect, but also greatly extend the service life of water-based cutting fluid, reduce waste liquid emissions, and obtain greater economic benefits. Cutting fluid is an auxiliary material in the process of cutting (including grinding), and also an auxiliary means to improve the processing conditions and effects. Rational use of cutting fluid can effectively reduce friction in the cutting process, improve heat dissipation conditions, reduce cutting force, cutting temperature and tool wear, improve tool durability and cutting efficiency, ensure the quality of machined surface and reduce the processing cost of products.