What is rust preventive oil? Rust often refers to the corrosion of ferrous metals in the air due to the electrochemical action caused by the participation of water and oxygen. Rust preventive oil is mainly used to form a protective film on the metal surface to isolate water and oxygen so as to play the role of rust prevention.
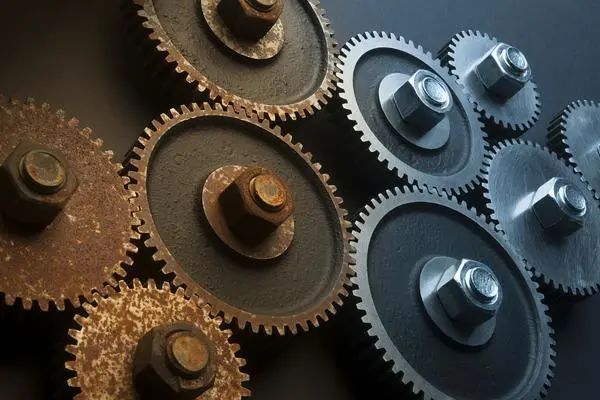
Classification of Common Anti rust Oils for Machining Mechanical Parts
1. Thin layer of antirust oil The oil film is thin and the amount of oil used is small. A thin antirust film is formed on the surface of the workpiece, which does not affect the appearance of the product. It is easy to clean and has good antirust performance. It is applicable to the antirust and preservation of parts and components in the automotive, hardware and electronic industries. 2. Replacement antirust oil With dehydration performance, it is suitable for products that have not been completely dried after the cleaning of workpieces. It can replace the water and then be cleaned easily. It is commonly used for rust prevention between processes and sealing for rust prevention. 3. Hard film antirust oil It has excellent antirust performance in humid and salt fog environments, and is generally suitable for working conditions with high requirements for antirust performance in harsh environments such as marine transportation, hull, steam chassis and equipment. 4. Water based rust inhibitor It is used for mixing water with low cost. It is widely used for rust prevention between ferrous metal, alloy steel and nonferrous metal products with short rust prevention period.
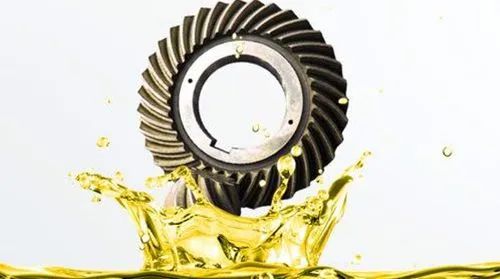
Selection of antirust oil 1. Select according to the product material: Different metal materials have different requirements for antirust oil. For example, cast iron and copper have different requirements for antirust. 2. Select according to the rust prevention cycle: For short-term rust prevention, rust preventative oil with a smaller viscosity and a thinner oil film can be used. For long-term rust prevention, rust preventative oil with a higher viscosity and a thicker oil film is required, 3. Select according to product structure and use mode: For example, for smaller products, immersion rust prevention can be used, and for larger products with complex structures, spraying or brushing can be used to prevent rust. No matter which method of use, it should be ensured that each part has formed an effective rust prevention film, Avoid local corrosion (in addition, it should be noted that the operator's hands should not directly contact the metal surface, and human sweat contains chloride ions, lactic acid and other rust causing substances, which are easy to form fingerprints on the surface of the workpiece). 4. Select according to the subsequent processing technology and assembly requirements: Such as the processing technology, storage environment, packaging conditions in the later stage, and whether cleaning is required before assembly.
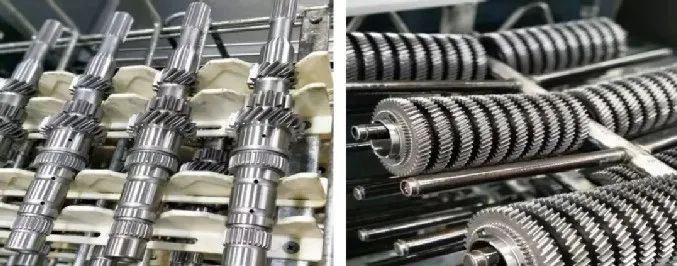
Usage of antirust oil and precautions 1. Immersion method: The advantage is that it can form a uniform anti rust film on the surface to ensure the complete coverage of the product, and the cost is low. The disadvantage is that it is only applicable to small products. Low viscosity anti rust oil is used, and the soaking tank must have a good drainage system. 2. Spray method: it is applicable to large and complex products. High efficiency spray must be used. It is easy for the product to fail to form an antirust film completely. The working environment requires good ventilation performance when using it. 3. Brush coating method: This method is simple to use, but it must ensure that every position of the workpiece is brushed, and the brush must be kept clean before use. 4. Flushing method: high efficiency, recycling, can save costs, but the products in the tank need to be drained and replaced regularly to avoid excessive moisture and other substances affecting the rust prevention effect. The above points are some basic knowledge about the selection and use of antirust oil. It is still easy to use antirust oil and rust during the production process. Common reasons are: too much water on the surface of the workpiece, the workpiece fails to form an antirust film, the antirust oil has not been replaced after a long time of use, a large amount of water and dust remain in the oil, and the workpiece surface is packaged before the antirust film is completely formed, Water vapor condensation caused by temperature difference in the package, more serious corrosion, packaging materials or quality not meeting the process.