In the process of daily reading literature or discussing problems, we often encounter some nouns and terms. Most of the time it is self-evident, but sometimes it is not clear. Many terms have been established by convention and are difficult to change. It is important to define them clearly and understand their connotation. The process of clarification will help deepen the understanding of relevant concepts and theories.
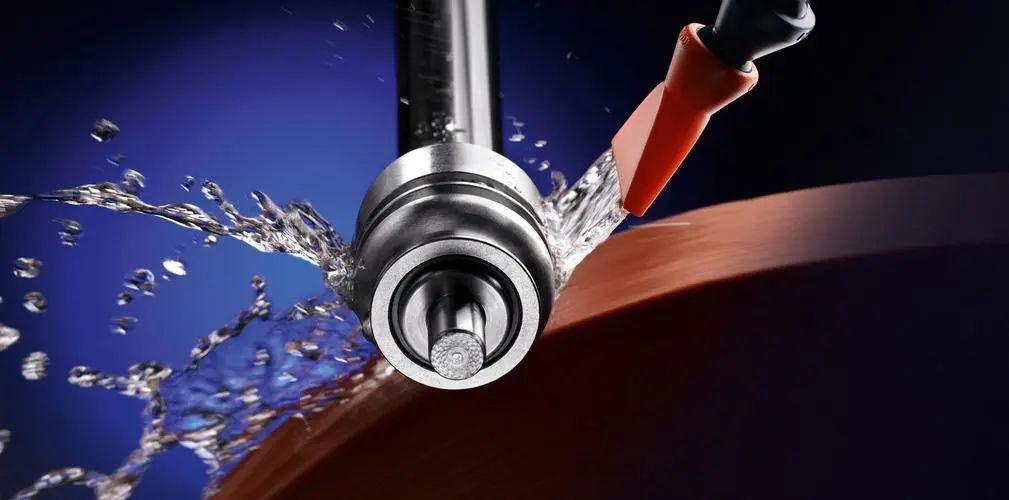
1. Emulsion, semi-synthetic liquid, synthetic liquid Emulsion is generally defined as a macroscopic uniform system with oil phase distributed in water formed by diluting the stock solution with more than 50% oil content. Those without mineral oil are called synthetic liquid, and those between them are called semi-synthetic liquid or microemulsion. The definition of synthesis is to change a substance with simple composition into a substance with complex composition through chemical reaction. Obviously, the synthetic fluid and semi-synthetic fluid mentioned here have nothing to do with whether synthesis has been carried out, and there is no corresponding chemical basis to call them synthetic fluid or semi-synthetic fluid. Semi-synthetic liquid should be called as emulsion with less oil (usually less than 20%) or stable emulsion. According to the size of its solute, the synthetic solution should be called colloidal solution in the colloidal range (usually less than 0.1-1 μ m); At the molecular scale, it should be called solution, and some people call it "true" solution. It is silly to think whether this adjective is necessary, because in the future, if there is no word "true" in the front, it seems to be false. In steel rolling oil, compared with emulsion, it is also called synthetic liquid, but it actually refers to replacing animal and vegetable oil with lubricating ester. The size of oil phase in emulsion does not change (generally more than 2 microns). Naturally, by the same token, it is not necessary to call it synthesis. The reason why it is called synthetic liquid may be that all the components used are synthetic esters without animal and vegetable fats. In fact, the Chinese character "ester" has clearly indicated that it is obtained by chemical reaction, rather than natural animal and vegetable oils "fat", so it is no longer necessary to call it synthetic ester, just as we do not have to call any products obtained by chemical reaction "synthetic", such as "nylon" as "synthetic nylon". It is appropriate to call lubricating ester because its function is lubrication, which is different from emulsified ester. Whether the hydrotreated Base Oil should be called synthetic oil has been debated for decades, and there is no final conclusion. Strictly speaking, hydrotreating is to restructure the structure of crude oil products by chemical methods. Hydrogenated base oil should be called synthetic oil, but it is not included in the current popular statement. According to the classification of API (American Petroleum Association), Class I oil refers to traditional solvent refined oil, Class II oil and Class III oil are hydrotreated, and Class IV oil is used to refer to synthetic oil, such as PAO (poly α- Olefin synthetic oil), Class V oil is other base oil except for the above four categories. In addition, the emulsion used in the cutting and grinding process is not mineral oil but vegetable grease or lubricating ester. Although its oil drop size is the same as that of the normal lotion, it is also called synthetic liquid, which is the same as that of steel rolling oil called synthetic oil, but its content is not as high as that of steel rolling oil. The above statements are quite popular in the industry. It is impossible and unnecessary to completely change them, but it is important to understand the true meaning of "synthesis". 2. Micro emulsion As mentioned above, it is suggested that semi synthetic liquid be called micro lotion or micro emulsion, which is reasonable to some extent, because the small oil content and the added emulsifier result in small oil particles, generally 0.5-1 µ m. It is widely believed in the industry that micro emulsion takes into account the advantages of emulsion (good lubrication ability, good antirust performance and easy waste liquid treatment) and the advantages of (synthetic) solution (stable and good cleaning and cooling performance), It represents the important development direction of metalworking fluid. Although the terms are the same, it should be pointed out that the microemulsion mentioned here is completely different from the microemulsion mentioned in colloidal chemistry. The microemulsion mentioned here still belongs to the category of emulsion and is thermodynamic unstable, but the microemulsion in colloidal chemistry is thermodynamic stable. The relevant differences are shown in the table below. The microemulsion in colloidal chemistry is linked with the solubilization of surfactants. It is thermodynamic stable and completely different from the concept of microemulsion we talked about here. It is closer to the colloidal solution mentioned earlier. 3. Cutting, grinding and forming The forming principle of machined surface in cutting and grinding mainly includes: 1) tool tip path method; 2) generation method; 3) Forming method. The tool path method is easy to understand. The generation method is actually the gradual processing of the tool on the envelope surface in a pure rolling way. The forming method directly processes the metal into the shape of the forming tool, but it is not usually called the forming method. Similarly, in the process of forming, some processes do not necessarily process the workpiece to the tool shape, such as free forging, but we still call it forming process. Some people divide metal processing into big chip processing, micro chip processing and non-chip processing according to whether there are processing chips. It is quite reasonable. Cutting usually produces large chips, grinding is microchip processing, and forming processing is chip-free processing. There are two basic laws, namely, the law of volume equality and the law of minimum resistance, in the process of chip free machining or forming. The law of volume equality, also known as the law of mass conservation, refers to the volume or mass equality before and after processing, while the law of minimum resistance refers to the flow of metal particles along the direction of minimum resistance during processing. 4. Quenching medium and quenching cooling medium It is often said that there are four kinds of heat treatment: normalizing, annealing, quenching and tempering. Their common feature is to heat the metal to a certain temperature, hold it for a certain time, and then cool it down at a certain speed, including three stages of heating, holding and cooling. The difference between the four fires in the cooling stage is that normalizing is usually cooled in the air, annealing is usually cooled in the furnace, tempering is usually also cooled in the air, only quenching is special, and its cooling speed is usually the fastest, such as cooling in water or oil. The purpose of rapid cooling is to make the carbon dissolved in the steel matrix structure (austenite) at high temperature remain in the lattice without diffusion, and obtain the distorted supersaturated solid solution structure, that is, to achieve the purpose of strengthening. Quenching also includes three stages, namely quenching heating, quenching heat preservation and quenching cooling, but in many cases quenching is only equivalent to quenching cooling, and the oil and polymer used for quenching cooling are also called quenching medium. Obviously, in a complete sense, it is more accurate to call quenching cooling medium, because there may also be quenching heating medium and quenching insulation medium in the quenching process. The room temperature structure of aluminum is different from that of steel. It is a face-centered cubic structure. Although it is also a supersaturated solid solution after quenching, it cannot be strengthened. It needs to be strengthened until the coherent or semi-coherent precipitates precipitated in the subsequent heating (artificial aging) or placing (natural aging) process cause distortion. Therefore, although we sometimes call it aluminum quenching, it is actually different from steel, and it can be strengthened in the process of quenching. Many people call it solution treatment for this reason. The solution treatment is to prepare the structure for aging strengthening. It includes three processes: heating, heat preservation and cooling. The corresponding quenching medium is more accurately called solution cooling medium or quenching cooling medium. 5. Gray iron and gray cast iron In the iron-carbon phase diagram shown below, steel with carbon content below 2.11% and iron with carbon content above 2.11%. The dotted line in the figure shows that C exists in the form of graphite, while the solid line shows that carbon forms cementite (Fe3C), which is more stable than cementite. If the cementite is heated for a long time, it will decompose into graphite.
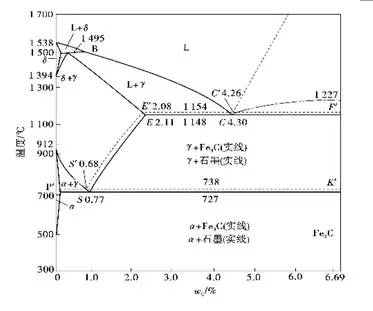
If graphitization is carried out sufficiently in the casting process, and carbon will exist in graphite state, the fracture of cast iron will be gray black, which is called gray cast iron; On the contrary, if graphitization is not carried out sufficiently, carbon exists in the form of Fe3C, and the fracture surface of cast iron shows white bright color, which is called white cast iron, and between the two, is granulated cast iron. For gray cast iron, if the graphite is distributed in flake form, it is called gray cast iron for short, and it is distributed in spherical form, it is called nodular cast iron for short, and it is vermicular cast iron if it is distributed in vermicular form. It can be seen that gray cast iron is opposite to white cast iron, and gray iron is one of the gray cast iron, which is included in gray cast iron. Grey iron is not equal to grey cast iron.