In order to improve product quality and productivity, the workshop has purchased several five axis CNC machining centers. In the past, the workshop used simple CNC machine tools. After using the five axis CNC machining center, the workshop continued the previous method of cutting fluid management. After using the five axis CNC machining center for a period of time, several machining centers failed one after another. After maintenance by the manufacturer, it was found that the electrical pipeline of the machine tool spindle and the built-in system had serious corrosion caused by the cutting fluid, which caused the hidden failure of the electrical system of the equipment, and the failure shutdown had seriously affected the normal production and delivery. Today, we focus on the analysis of machine tool corrosion, and propose effective control measures to avoid machine tool corrosion. Main corrosion of machine tool 01 Main shaft electrical pipeline corrosion Internal corrosion of main shaft
When the equipment manufacturer repaired and disassembled the spindle, it was found that there were some yellowish brown substances attached to various electrical pipelines, the metal surface had been rusted, the outer rubber of some electrical pipelines had been corroded, hardened and peeled off, and the internal part of some pipelines had entered the cutting fluid. After fault analysis, it was found that it was related to the cutting fluid. Because the internal structure of the spindle pipeline is complex and the corrosion degree has caused hidden trouble, the pipeline needs to be replaced as a whole. However, the import cycle of machine tool accessories is long, resulting in long time shutdown for maintenance and large losses. 02 Rust problem of machine tool After the equipment was disassembled in case of failure, it was found that some corrosion had occurred inside the machine tool. One X-axis ball screw was seriously rusted. In order to ensure the machining accuracy, it is impossible to assess the impact of corrosion on the machine tool in the future.
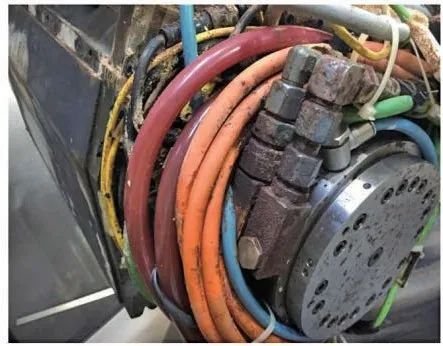
03 The machine tool has crystal problems There are some crystalline substances on the gap and surface of the machine tool, and the formation mechanism needs to be analyzed. These crystalline substances have strong adhesion and are difficult to remove. After the maintenance of the equipment manufacturer, it is analyzed that they have corroded the surface of the machine tool, and there is a hidden danger of reducing the sealing performance.
Crystallization
Causes of Machine Tool Corrosion Caused by Cutting Fluid In view of the corrosion of the above machine tools, the specific processing conditions and the use of cutting fluid are analyzed as follows.
1) There are many impurities and rust in the processed workpiece
The machined workpiece belongs to large casting, with many impurities in the inner cavity and rust on the surface. After the work-piece passes the scribing and ordinary milling machine processes, it turns to the five axis machining process. In addition to the main functions of machining lubrication and cooling, the cutting fluid also brings a large amount of rust, sand, chips and other impurities to all parts of the machine tool. If rust or chips gather in the dead corners of the machine tool or cannot be washed off, they will stick to the machine tool parts, As a result, the cutting fluid or water vapor will condense in the adhesion between the rust or chips and the machine tool for a long time, and the machine tool parts will gradually be rusted, even the whole machine tool will be rusted. 2) Analysis of on-site water quality shows poor data of relevant indicators According to the water quality analysis of tap water collected on site, the content of chloride, hardness and sulfate ion is on the high side. For example, the conductivity of tap water is on the high side, and the content of chloride ion and sulfate ion is on the high side, so it is not suitable for mixing cutting fluids. If it is used for mixing cutting fluids, it will cause corrosion of machine tools and reduce the service life of cutting fluids. The filtered purified water, with low conductivity and ion content, is suitable for mixing cutting fluids, which can extend the service life of cutting fluids and reduce the risk of machine tool corrosion. 3) Formation reason of crystal residue First, the content of calcium and magnesium ions in the water is high, and the ability of the cutting fluid to resist hard water is poor, which causes the soap of the cutting fluid to precipitate and stick to the machine tool parts for a long time, forming crystals. Second, in order to draw a clear line on the workpiece blank, the workshop marking process has been painting a layer of white lime water on the surface of the blank. Long time application has made a large amount of lime water mixed in the cutting fluid, and the hardness of the cutting fluid has increased, leading to the precipitation of the cutting fluid soap, resulting in the deposition of scaling substances with strong adhesion and difficult to remove at the machine tool seal, resulting in the decline of the sealing performance of the machine tool.
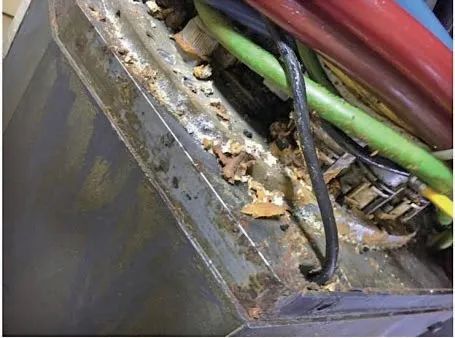
4) Unclear cutting fluid selection standard Before purchasing five axis CNC machining centers, most workshops used emulsion and cutting fluid with low cost. From workshop equipment managers to field operators, they did not attach great importance to the brand selection, model selection and index requirements of cutting fluid. 5) Long term lack of detection of cutting fluid status on site In the production process, the operator initially prepared and tested the concentration according to the cutting fluid proportion requirements until the next time the cutting fluid was degraded and replaced. During this period, the daily inspection of the cutting fluid concentration and PH value was not strictly carried out, so there was a problem in the use and management of cutting fluid on site.
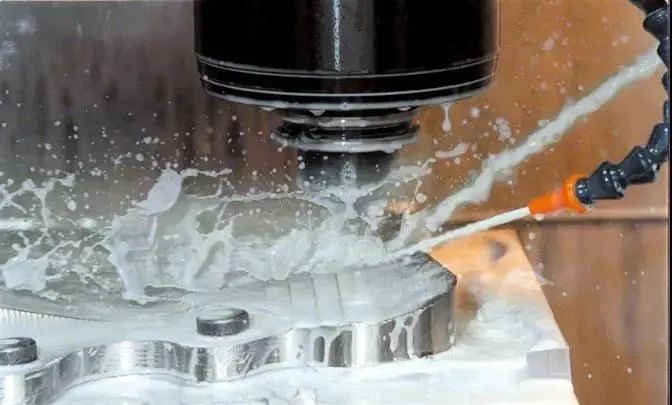
Measures to eliminate and control machine tool corrosion According to the causes of machine tool corrosion, the following specific fire control measures shall be taken for rectification. 1) Add process requirements. Before production and processing of workpieces, add shot peening process to eliminate rust, sand and other impurities. 2) Lime water will not be used in the marking process to eliminate the corrosion of equipment caused by lime deposition. 3) Select a cutting fluid with high comprehensive performance and good antirust performance through comparison test of several cutting fluids. 4) Prepare cutting fluid with purified water instead of tap water. Although the cost has increased, it can improve the comprehensive performance index of the cutting fluid, extend the service life of the cutting fluid, and play a good role in the rust prevention of the equipment. 5) Establish a regular inspection system for cutting fluid and keep records. The operator is required to regularly inspect the cutting fluid concentration, PH value and other indicators. If the cutting fluid deteriorates, it needs to be replaced in time, and new fluid should be added according to the concentration change to ensure the quality of the cutting fluid. 6) It is stipulated that the cutting fluid manufacturer shall regularly detect the bacterial content, chloride ion content and other indicators, and assist and guide the operators to monitor the cutting fluid indicators. 7) Carefully check the status of the cutting fluid filtering device of the equipment every day to ensure its normal operation; Clean the cooling system at least twice a year, and use system cleaning agent for cleaning. 8) Regularly inspect the sealing performance of the equipment, and timely repair and handle problems found to prevent cutting fluid from entering the machine tool. 9) Clean the tool magazine, workbench and other parts that are easy to retain cutting fluid with cutting fluid regularly to avoid corrosion.
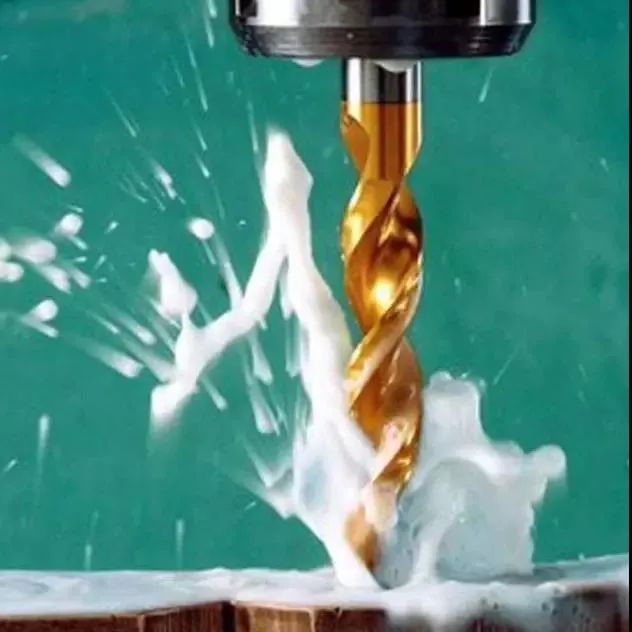
Through the summary and analysis of the above cases of cutting fluid corrosion on machine tools, it can be concluded that the use and management of cutting fluid were not paid attention to in the workshop, resulting in the breakdown of high-end equipment and affecting the normal delivery of production. After the corrosion of the machine tool appeared, the workshop and the manufacturer jointly diagnosed and analyzed the problem, and took effective fire control measures in time. At present, after more than one year of production and operation with proper cutting fluid, the equipment of the five axis CNC machining center operates normally, and there is no machine tool corrosion problem that existed before. This further proves that selecting the appropriate cutting fluid can eliminate the hidden danger of corrosion caused by the cutting fluid on the machine tool, significantly reduce the equipment failure rate, improve the equipment utilization rate, and ensure the safe operation of the equipment.