1. Suppression and destruction of foam 1) Since the foam is a thermodynamically unstable system, the foam will eventually be destroyed. The main causes of bubble collapse are the thinning of the liquid film and the diffusion of gas in the bubble.
a. When the liquid film is thick, the liquid film existing between the bubbles, because the density of the liquid phase is much greater than the density of the gas phase, will produce a downward discharge phenomenon under the action of gravity, making the liquid film thinner and stronger It also falls, and it is easy to rupture under external disturbance, causing the bubbles to coalesce. At the boundary of the polyhedral foam, the drainage of the liquid film is dominated by surface tension.
b. The radius of curvature of the small bubbles is small, the pressure in the small bubbles is greater than that in the large bubbles, the small bubbles will be exhausted into the large bubbles through the liquid film, so that the small bubbles become smaller and disappear, the large bubbles become larger, and the liquid The membrane also becomes thinner and eventually ruptures.
c. The bubbles on the liquid surface, the pressure in the bubbles is higher than the atmospheric pressure, and can be directly exhausted to the atmosphere through the liquid film, and finally the bubbles burst.
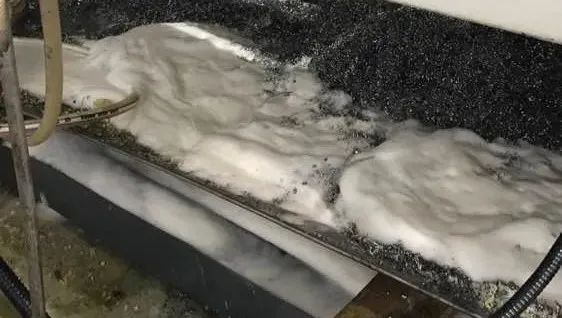
2) There are two main ways to eliminate foam, mechanical method and the use of defoamer
a. The mechanical method uses physical action, and the foam is broken by strong mechanical vibration or pressure change. This method does not require the introduction of foreign substances, but the efficiency is not high, and it has little effect on the fluid-type foam with high viscosity, nor can it eliminate the root cause of foam stability. as a helper method when necessary b. Defoamers destroy the foam by replacing the surface film that forms the foam with a completely different type of film, or increase the drainage rate of the film in the foam, shortening the life of the foam. Defoamers are divided into foam breakers and foam suppressors. The agent pushes or squeezes the surfactant molecules of the liquid film, and directly breaks the generated foam. It has an excellent foam breaking effect at the moment of contact with the foam, but when it is dissolved, it loses its effect and cannot be inhibited. Foam regeneration is a temporary defoamer. Foam suppressors work by reducing the surface tension of small localized areas to very low values, thinning these areas rapidly, under the traction of surrounding areas of higher surface tension. Foam burst, can inhibit and prevent the formation of foam, is a continuous defoamer. Generally, each defoamer is formulated with a variety of ingredients. An excellent defoamer must function as both a foam breaker and a foam suppressor at the same time. General organic compounds, such as hydrocarbons, ethers, alcohols and phosphate esters, have larger spreading coefficients, stronger foam breaking effects, and poor foam suppressing effects. Silicone emulsion defoamer is both. c. Some antifoaming agents lose their effectiveness after being added to the solution for a certain period of time. To prevent the formation of foam, some antifoaming agents need to be added. The reason for this may be related to whether the CMC of the foaming agent (surfactant) in the solution is exceeded. In surfactant solutions that exceed CMC, defoamers (usually insoluble organic liquids) may be solubilized so that they lose their ability to spread on the surface, reducing the effect of defoaming. However, the defoaming effectiveness of the defoamer is affected. Reduction or even loss of activity, in most cases, is due to the change of the dispersion state and surface properties of the defoamer itself. Perforate, burst or merge. The particle diameter is similar to the foam thickness, and the effect is better. Due to the repeated action of the defoamer particles, repeated crushing will reduce the particle size of the defoamer. In addition, due to the influence of the foaming agent, especially the "affinity" with the foaming liquid, the antifoaming agent particles become too small and lose the activity of the antifoaming agent particles in the foaming liquid. The exercise status also has an effect on the defoaming efficacy. If the defoamer particles are too large, the movement of the defoamer particles will be sluggish, and the defoamer particles cannot be quickly aggregated to the air-liquid interface of the bubble film to act, resulting in poor activity. It is possible to merge and become larger. At the same time, the defoamer gathers on the bubble film. When the continuous foam surges from the liquid to the surface, it adheres to the bubbles like "flotation", and concentrates the defoamer particles distributed in the liquid to the surface. In the foam layer on the liquid surface, and after the foam bursts, it turns into a small amount of liquid, and a large number of defoamer particles gather in a small amount of liquid, and it is easy for the defoamer particles to coalesce. In addition, the active ingredient of the defoamer will also adhere to the wall of the container, and the surface properties of the defoamer particles will often change due to the adsorption of the foaming agent. From lipophilic to hydrophilic, the activity of the defoamer decreases and loses Antifoaming effect. 2. Foam problems and solutions during the use of cutting fluid There is a lot of foam in the cutting fluid, which will greatly reduce the cooling effect of the cutting fluid
1) The reason for the foam problem, the reason for the cutting fluid itself a. Most of the additives of cutting fluid are surfactant substances, which makes the cutting fluid (including all emulsions) tend to have different degrees of surface foaming under suitable stirring conditions b. The effect of anti-foaming additives in cutting fluid is not to prevent the tendency of foaming in cutting fluid, but to reduce the stability of the foam adsorption film and shorten the existence time of the foam. Foam prone to appear when anti-foam additives reduce effectiveness c. The smaller the viscosity of the cutting fluid, the easier it is to generate foam d. The anti-oxidative stability of the cutting fluid is poor, and it can also contribute to the generation of foam e. The water quality of the solution is too soft or contains alkali f. Reasons for high concentration system circulation g. The liquid level is too low, the pump produces holes h. The flow rate of the cutting fluid is too fast, and the bubbles have no time to overflow, and they accumulate more and more, resulting in a large amount of foam. i. The nozzle angle of cutting fluid is too straight Too many right angles in the tank design Too much line pressure High circulation rate (low cutting fluid volume), excess pressure differential in suction and overflow conditions j. The positioning of the hydrocyclone separator for separating solid particles is incorrect, the cutting is carried out by the hydraulic transmission of the cutting fluid nozzle, the sealing of the fluid circulation pump is not strict, and the resistance of the oil pipe forms a jet. 2) How to eliminate the bubble problem a. Ensure the liquid level height and eliminate pitting corrosion b. Exclude mechanical and system circulation reasons c. Check the nozzle and improve the spray pressure d. Adding/supplementing suitable defoamer In the case of soft water, by making the water hardening to improve the condition, calcium acetate can be added to increase the hardness.