What are the causes of black spots and rust on the workpiece?
How to protect the "fragile" workpiece surface?
What is the relationship between metalworking fluid and metal corrosion?
Although there are various causes of corrosion, not all types of corrosion will occur at the same time. Before anti-corrosion and antirust treatment of workpieces, it is necessary to know the following information about metal corrosion: In actual metal processing, several kinds of corrosion will occur at the same time; The causes of corrosion are often various, but only one thing can prevent further corrosion; It is impossible to prevent all metals from corrosion. If the metal surface to be cut remains in the air, it will also encounter oxidation (corrosion). It should be ensured that the corrosion is kept within an acceptable level; Almost all corrosion in water environment has electrochemical corrosion components. The situation of metal corrosion is complex, but the electrochemical corrosion is the most closely related to the Metal Working Fluid. Metal working fluid is conductive liquid, which belongs to electrolyte to a certain extent, leading to electrochemical corrosion in the process of machining. Corrosion problems are easy to prevent and difficult to remove. Therefore, adding Corrosion Inhibitor in the medium to prevent or slow down corrosion is an economical and simple method.
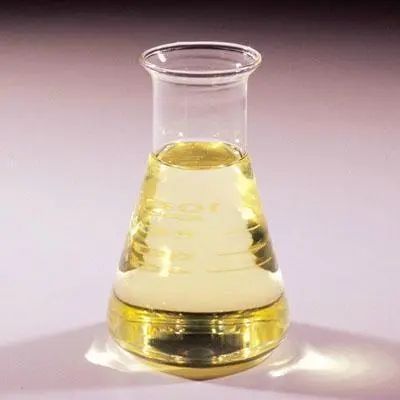
Classification of corrosion inhibitors: 1. It can be divided into organic corrosion inhibitors and non organic corrosion inhibitors according to chemical composition. 2. It can be divided into water solution, oil soluble and vaporizing corrosion inhibitors according to the use state. 3. According to pH value, it is the corrosion inhibitor of neutral solution and acidic solution. 4. According to the action mechanism of corrosion inhibitors, they are divided into anode type, cathode type, adsorption type and protective film type. Selection principle of corrosion inhibitor 1. Different corrosion inhibitors shall be selected for different corrosion media. The neutral water medium mainly adopts passive (anodic) and precipitation corrosion inhibitors, most of which are inorganic. Adsorption type corrosion inhibitors, which are mostly organic substances, are used in acidic media. Oil soluble adsorption type corrosion inhibitor is used for oil medium to eliminate water adsorption and play a protective role. 2. Different corrosion inhibitors are used for different metals. The inhibition effect of single type corrosion inhibitor is smaller than that of composite corrosion inhibitor. Therefore, few single type corrosion inhibitors are used in modern corrosion inhibitors, but composite corrosion inhibitors. Many efficient corrosion inhibitors are often toxic. For example, chromate is an efficient oxidizing corrosion inhibitor in neutral water medium, with pH value of 6~11. In addition to steel materials, it can also effectively protect most non-ferrous metals. Chromate is toxic, harmful to the environment, and its use is limited. Corrosion inhibitor in neutral medium Neutral medium solutions include various kinds of water (such as cooling water, boiler water, washing water, heating water, recycled sewage, etc.), neutral brine solutions (such as aqueous solutions containing NaCI, MgCl2, NH4CI, Na2SO4, Na2CO3), and neutral organic solutions (such as oils, alcohols, polyhalogenated hydrocarbons, etc.). Circulating cooling water is the most widely used corrosion inhibitor. Corrosion inhibitor for industrial circulating cooling water 1. Inorganic salt corrosion inhibitor 1) Chromate has good corrosion inhibition effect. Na2Cr2O7 or K2Cr2O7 are commonly used as passive (positive) corrosion inhibitors. Fe2O3 and Cr2O3 oxide films with a thickness of several nanometers (nm) were formed on the steel surface. The critical content of chromate forming passivation film in water is 10E-4~1.3x10E-4 (mass fraction). When the concentration of CI - in the liquid increases or the temperature increases, its critical content also increases, otherwise local corrosion will occur. It is difficult to prevent local corrosion when chromate is used alone, and it is often used in combination with polyphosphate or zinc salt. Corrosion inhibition effect of (30 ℃) The composite corrosion inhibitor of chromate and polyphosphate has good corrosion inhibition effect on carbon steel, Cu, Cu Zn alloy, Al and stainless steel when the water temperature is below 100 ℃ in circulating cooling water and seawater. Chromate is toxic and needs to be treated to make the content of Cr2+not exceed 0.05~0.1mg/L. Therefore, there are few or no chromates used as corrosion inhibitors. 2) Polyphosphate corrosion inhibitor is often used in combination with zinc salt and other corrosion inhibitors to improve the corrosion inhibition effect. The commonly used polyphosphates are sodium tripolyphosphate and sodium hexametaphosphate. Sodium hexametaphosphate has good corrosion inhibition effect, while sodium tripolyphosphate is used more because of its low price. Sodium hexametaphosphate has significant corrosion inhibition effect in water with dissolved oxygen, promoting the formation of steel surface γ- Fe2O3 passivation film is an anodic corrosion inhibitor. When Ca2+and Zn2+ions are contained in the water, the inhibition effect of polyphosphates will be affected. Only when [Ca2+/(NaPO3) n] is greater than 0.2, the inhibition effect will be good. Polyphosphate is easy to hydrolyze, and its main disadvantage is that it reduces the corrosion inhibition effect after hydrolysis. 3) The composition of silicate corrosion inhibitor is Na2O · nSiO2. When n=3.3 in water with pH>6, n=2 in water with pH<6 is more appropriate. Silicate is a precipitation corrosion inhibitor. Ca2+can improve the corrosion inhibition effect of silicate, and silicate forms insoluble protective film with Ca2+and Mg2+ions. It should be pointed out that when sodium silicate corrosion inhibitor is used, the concentration of Ca2+and Mg2+ions in water cannot be too high, otherwise there is a risk of calcium silicate and magnesium silicate scaling. When the content of Mg2+in water is greater than 250mg/L, sodium silicate corrosion inhibitor should not be used. When sodium silicate and zinc salt are used together, the corrosion inhibition effect can be improved. The advantage of sodium silicate corrosion inhibitor is non-toxic and cheap. 4) Molybdate corrosion inhibitor belongs to anode type, which can form passive film on the surface of carbon steel in the presence of dissolved oxygen. The commonly used molybdate is Na2MoO4. When molybdate is used alone, the addition amount should reach 4x10E-4 (mass fraction). Therefore, combined use with organic phosphate and zincate can reduce the amount of molybdate and improve the corrosion inhibition effect. Molybdate has significant effect on inhibiting pitting corrosion and crevice corrosion. The dissolved molybdate ion can effectively passivate the iron in the etch hole and reduce the oxide accumulation. Molybdate is a promising corrosion inhibitor with low toxicity and strong adaptability. 5) Other inorganic salt corrosion inhibitors, such as nitrite (NaNO2, KNO2), are anodic corrosion inhibitors. When the addition amount reaches (25~50) x10E-6 (mass fraction), they have good corrosion inhibition effect. Nitrite is easy to decompose in acidic medium with pH<6 and has no corrosion inhibition effect. When pH=9-10, the corrosion inhibition effect is the best. Sodium nitrite is easy to turn into carcinogen, which is harmful to human health, and should not be used. Zinc salt corrosion inhibitor is a component of composite corrosion inhibitor, belonging to precipitation type and cathodic type. Zinc salt is toxic, and its dosage should be limited within the specified range of sewage discharge, so the dosage often used is only (3~5) x10E-6 (mass fraction). 2. Organic salt corrosion inhibitor
1) Organic phosphoric acid, phosphate and phosphate ester.
This type of corrosion inhibitor has the ability of complexing metal ions, forming a complex precipitation film on the metal surface, and has a corrosion inhibition effect on the metal. When the content of organic phosphoric acid inhibitor is high, the inhibition effect is greater than that of inorganic phosphate, for example, the content of HEDP and EDTMP is 100 × The corrosion inhibition effect of 10E-6 (mass fraction) is 4-7 times greater than that of polyphosphate. If organic phosphoric acid and inorganic phosphate are used together, the corrosion inhibition effect is better. Organic phosphoric acid has high chemical stability, is not easy to hydrolyze, can withstand higher temperatures, has good scale inhibition ability, and is a promising corrosion inhibitor. 2) Organic hydroxy acids Inhibitors used in neutral water medium include aromatic carboxylic acid, aliphatic substituted carboxylic acid (such as hydroxy acid, amino acid and amide carboxylic acid) and its sodium salt. For example, the raw material of acyl sarcosine is easy to obtain, non-toxic, and does not produce environment. Pollution, applicable to soft water or hard water medium with pH=6~11. In addition to cooling circulating water, boiler water, brine system, blast furnace and converter cooling water can be used, which is a promising corrosion inhibitor. Corrosion inhibitor in neutral saline solution Neutral salts dissolved in water, such as NaCI, KCI, MgCl2, CaCl2, Na2CO3, Na2SO4, etc., can promote metal corrosion. Most of the corrosion inhibitors used in the cooling water system can also be used as corrosion inhibitors of neutral saline solution. However, when the salt content is high, the inhibitor with better corrosion inhibition effect should be selected. 1. Alkyl amino alcohols Alkylamino alcohol has a good corrosion inhibition effect on carbon steel in NaCl and CaCl2 aqueous solutions, and the corrosion inhibition rate can reach more than 90%. Table 5 shows the corrosion inhibition effect of 2-ethylaminoethanol on carbon steel in 3% water solution of w (NaCI). With the increase of its content, the corrosion inhibition effect increases, and the pH value also increases. When the content is 3. 1x10E-4, pH=10.3, and then when the content of corrosion inhibitor is increased, the pH value remains unchanged. If NaOH is added to adjust the pH value, certain corrosion inhibition effect can also be produced. 2. Zinc gluconate It is found that zinc gluconate (C4H11O17) 2Zn has a good corrosion inhibition effect on carbon steel in seawater, and also on copper in seawater. The concentration of zinc gluconate has an impact on the corrosion inhibition effect. When the content reaches 4x10E-3 mol/L, the corrosion inhibition rate can reach 60%, and when the content continues to increase, the corrosion inhibition effect decreases.