Purpose of cutting fluid During the cutting process, high temperature and high pressure are produced at the cutting part due to severe friction, which seriously affects the service life of the tool, the precision and surface finish of the machined part. There are two main measures to reduce temperature, reduce friction, ensure tool life and workpiece accuracy: (1) Reduce friction during cutting and reduce tool wear; (2) Take away the high temperature gathered in the cutting part in time. The traditional lubrication method is to spray cutting fluid to the machining point. According to experience, the greater the supply of cutting fluid, the better the effect. In the past few years, "high pressure cooling" was actively promoted in the field of cutting. For a time, a large supply of cutting fluid was regarded as the "savior" of cutting.
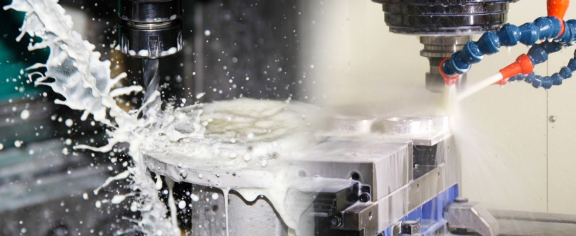
Hazards of using cutting fluid Since the 20th century, the machinery manufacturing industry has undergone new changes: (1) The world has paid extensive attention to environmental protection issues such as global warming, the destruction of the ozone layer and the generation of dioxins; (2) Concern about the health hazards caused by the additives in the cutting fluid to the operator, and the safety hazards caused by the leakage and dispersion of the oil agent to the operator; (3) Pay attention to the environmental pollution caused by waste oil treatment, and the public opinion strongly demands that the cutting fluid must meet the environmental protection requirements.
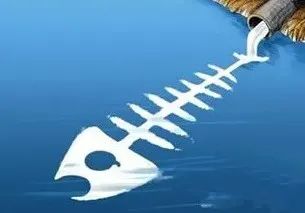
In this context, European and American countries and Japan have formulated or revised the waste oil treatment law, the mobile registration law for the emission of environmental pollutants, and the dioxin special treatment law. As a result, although a large amount of cutting fluid can receive better lubricity, higher processing quality and processing efficiency, according to the requirements of environmental protection, the cutting waste must be treated innocuously before it can be discharged. The new requirements have greatly increased the cost of cutting. According to the survey of a German automobile factory, the tool cost accounts for 2%~4% of the total production cost; The cost related to cutting fluid accounts for 7%~17%, which is 3~5 times of the tool cost. The main shaft rotation accounts for 20% of the energy consumption of the machining workshop, while the energy consumption related to cooling accounts for 53%. To sum up, the uncontrolled use of coolant to reduce tool and energy consumption can only be counterproductive. Modern lubrication technology 1. Dry cutting method Dry cutting without cutting fluid can completely solve the environmental problems caused by cutting fluid. In recent years, with the rapid development of tool materials, the adaptable cutting temperature has increased significantly.
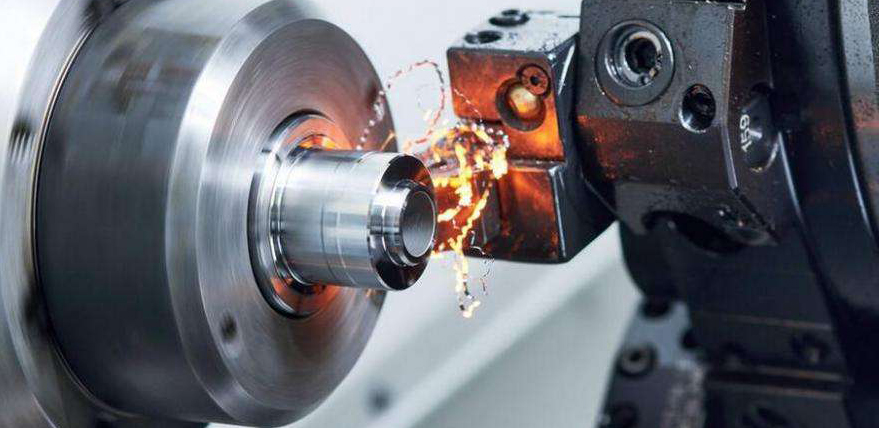
The traditional tool steel tools have a heat-resistant temperature between 200 and 300 ℃. Beyond this temperature, the hardness of the tools will drop significantly, and the tools will be quickly worn and discarded. High-speed steel tool, the maximum allowable temperature can reach 500~600 ℃; The cutting temperature of diamond tools can reach 800 ℃ (because the friction coefficient of diamond tools is very low and cannot be used for cutting ferrous metals, the temperature is low). Hard composite tool can still cut at 800~1000 ℃; Ceramic tools can be used to 1200 ℃; The service temperature of cubic boron nitride tool can reach 1400 ℃. The processing method, tool performance and material to be processed are well matched, and dry cutting is the simplest processing method. However, because dry cutting does not use cutting fluid, the friction coefficient is large, the cutting resistance is large, and the efficiency is low; In addition, the heat generated in the cutting process cannot be exchanged in time, resulting in the increase of the surface problems of the tool and the workpiece, and the workpiece is not easy to obtain high accuracy. 2. MQL cutting method The ideal method is to use the minimum amount of lubricant on the premise of ensuring lubrication and cooling performance and meeting environmental protection requirements. This processing method is called semi-dry cutting.
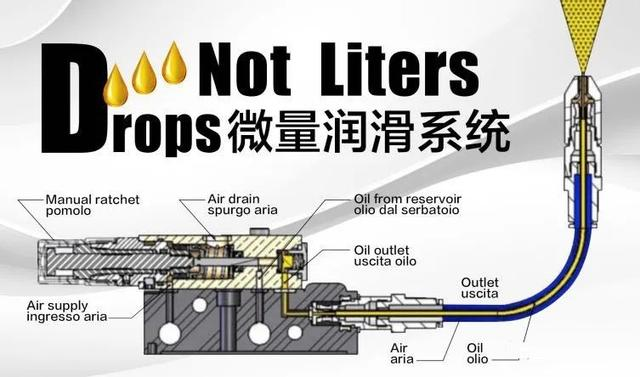
For semi-dry cutting, the supply of cutting fluid is small, which requires that the cutting fluid must be added to the cutting part practically and reliably. It seems that agricultural irrigation has developed from flood irrigation to sprinkler irrigation, and then to drip irrigation. A small amount of water is directly poured on the roots of crops.
In recent years, lubrication technicians have developed a series of new semi-cutting methods for environmental protection, energy conservation and high efficiency. For example, MQL machining method, floating nozzle method, megasonic cooling method, and their improved and compound semi-dry cutting technology. At present, the newly developed MQL (Minimum Quantity Lubricants) processing method has led to epoch-making changes in lubrication technology. The typical structure of MQL lubrication is shown in the figure below.
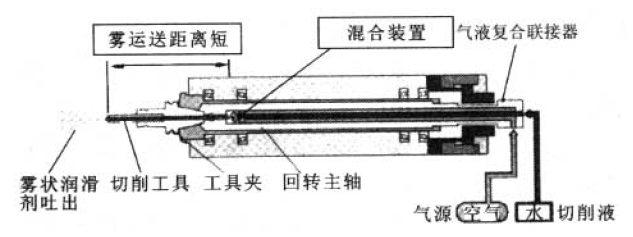
The structure is composed of the refitted machine tool spindle, oil supply system and air supply system. In the hollow spindle, a sleeve is placed, the inner tube is filled with oil, and the outer tube is ventilated. The oil and gas are mixed by the mixing device at the front end of the spindle, and the mist lubricant is input to the cutting tool. Because the rotating part of the mist lubricant is very short, it is not affected by the centrifugal force. The mist lubricant is efficiently sprayed through the hole at the front of the tool and accurately sprayed to the cutting part. The quantitative pump for oil supply is controlled by cNc (compound numerical contr01), and the oil supply quantity can be set arbitrarily. The fuel supply of MQL system is not more than 50mL/h; Compressed gas pressure is 0.2~0.4MPa. MQL processing has a series of advantages: (1) The oil consumption is small, only 1/20~1/50 of the traditional method. (2) There is almost no oil on the chip. (3) There is little oil attached to the workpiece, which can simplify the workpiece cleaning process. (4) The coolant circulation system that consumes a lot of energy is eliminated. (5) No complex lubrication management is required. (6) It is convenient to install MQL system on existing machine tools. According to the requirements of environmental protection and the characteristics of good lubricating performance and long service life of the oil required by the next generation of machine tools, MQL lubrication should use ester lubricating oil with good biodegradability, high bearing capacity, low evaporation loss and excellent oxidation stability. The use of ester oil in MQL lubrication method can solve the problems of lubrication performance and environmental protection. However, the cooling effect is not sufficient only by compressed air, so some improved MQL lubrication methods have been developed. For example, after atomizing oil and water respectively, spray them to the cutting point at the same time in a certain proportion. In addition, "water drop method with oil film", that is, oil, water and air are supplied simultaneously by multi-layer casing, so that a layer of oil film is attached to the surface of the water drop and sprayed to the processing part in the form of fog. The heat is taken away by the evaporation of the water drop for cooling, and the remaining oil film is used for lubrication and rust prevention. 3. Other micro-lubrication methods There are also floating nozzle method and megasonic cooling method (Megasonic cdolanf) for grinding process.